IoT in manufacturing: Turning hype into reality
There’s been a lot of hype around the industrial Internet of Things. For a long time now, it’s been predicted that the networking of assets through the use of sensors, software and connectivity will transform the way factories operate, and products are made. The use of IoT in manufacturing will make operations faster and more flexible, boosting their bottom line.
Well that’s the theory, anyway.
But just how close are we to turning this bold vision into reality?
How exactly has the industrial IoT helped manufacturers improve their productivity and efficiency? And what are the primary applications and business benefits?
The pace of digital transformation
To find out the answers to these important questions, Avnet Abacus recently curated research on the industrial IoT from a variety of sources, to help paint a picture of the current state of implementation.
The data casts a spotlight on the rate of adoption of IoT in manufacturing environments, along with the different types of use cases.
One study, taken from a survey of senior executives from 316 organisations that are implementing IoT initiatives, revealed that 62% of manufacturers are deploying IoT at full scale – across all regions, geographies and sites, for at least one application. This uptake shows that, for the majority of organisations, IoT has moved on from small-scale test projects to become a central part of their operations. Interestingly, the adoption of IoT initiatives at full-scale was far higher in manufacturing than any other sector, including retail and utilities.
As well as leading the way in implementation, manufacturing is expected to top spending on IoT solutions, reaching a total of $197 billion in 2019. Again, that beats sectors such as transportation and utilities which has significantly lower predicted spends.
This amounts to a serious level of investment in industrial IoT within manufacturing environments. But what benefit is that activity expected to deliver?
The study showed that reducing costs and improving processes were the top business drivers, followed by factors such as improving employee productivity and increasing competitiveness.
IoT uses and benefits
What is clear from the research is that the time for industrial IoT is well and truly upon us, with the C-suite increasingly recognising just how connected technologies can transform their businesses. So, with that in mind, let’s turn our thoughts to the main areas of impact. As a growing number of manufacturers have started to adopt industrial IoT, it’s possible to categorise the most common uses around six prominent themes.
1. Predictive maintenance
By using sensors and collecting data, in combination with big data analytics to spot patterns and trends, it’s possible to identify and prevent equipment failure before it occurs. Eventually, artificial intelligence and machine learning can also be deployed to drive totally intuitive condition monitoring methodologies with very little human input.
2. Continuous process improvement
The use of industrial IoT and real-time dashboards delivered to mobile devices provides manufacturers with far greater visibility of production line performance than ever before. This means plant managers can quickly identify inefficient processes such as bottlenecks, allowing them to make changes and improve overall equipment efficiency.
3. Smart energy consumption
Automated building management systems connect sensors, actuators, controllers and other equipment over one IP backbone, enabling the monitoring of energy usage from machinery, lighting, HVAC and fire safety detector systems. This information can be combined with broader datasets such as weather forecasting and real-time pricing of electricity to give a more informed view of building performance.
4. Supply-chain optimisation
Supply chains in the era of industrial IoT are faster, more flexible, and more transparent, with manufacturers having total visibility of their incoming and warehoused components. Meanwhile, networked machines give feedback on real-time production rates, which in turn drives more effective purchasing operations.
5. Equipment tracking
Imagine knowing the location of every asset – down to individual hand-tools – inside your manufacturing plant. That is what equipment tracking, delivered through industrial IoT, is bringing to the factories of the future. Connected tools can also be taught to ‘learn’ the task at hand, ensuring operational performance within pre-set parameters. This improves production quality and reduces the chance of operator error.
6. Connected products
Boost customer engagement and operations by creating products with smart components that collect usage data. By fitting sensors to products out in the field, valuable real-world data gained throughout the lifecycle can be used to drive future product refinement.
Challenges to further IoT adoption
This IoT-enabled architecture is also leading to the creation of new business models based on servitisation, where the manufacturer effectively leases a service or a solution rather than selling pieces of equipment. This new approach results in far more predictable revenues over longer periods of time
The emergence of these six main areas of impact shows that industrial IoT is driving business advantage across a wide scope of activities. However, while some forward-looking organisations have been quick to embrace the power of connected technologies, there are still plenty of companies that are holding back. Research from management consultants Bain and Company shows that this reticence is fuelled by concerns over the cost of adoption of industrial IoT, along with the challenge of integration with existing processes and systems. Other barriers to adoption include uncertainty over how to measure returns on investment and fears that the digitalisation process will be hampered by a lack of qualified staff.
So how do these organisations overcome concerns and get on the path to digitalisation? One means of kickstarting new industrial IoT projects is to follow some best-practice recommendations which help to deliver a structured and considered approach to implementation. Firstly, it’s important to define your ambitions from the outset, being realistic with expectations for first time adoption and establishing a clear roadmap of what you want to achieve. It’s also sensible to embrace industrial IoT gradually, with due consideration given to issues such as interoperability with legacy processes, which can minimise the risk of disruption to production lines that could result in downtime.
Also, teamwork is key: digital transformation is as much about people as it is technology, and good communication lies at the heart of any successful business change. People are likely to have different levels of IT abilities, and this needs to be carefully considered when outlining the scope of activity and allocating responsibilities.
And finally, be empowered by partnership. The route to digitalisation is not a journey that needs to be taken alone, and fortunately, support is at hand. Avnet Abacus, for example, can act as a trusted adviser on IoT deployment, with experts on hand to discuss factors such as wireless protocols, sensing capability and powering solutions. This is backed up by a breadth of products such as antennas, batteries, connectors and wireless charging modules.
The future is bright for IoT
It’s clear that industrial IoT is no longer some fuzzy future technology that holds the potential to transform manufacturing. It’s already here, right now – finding widespread adoption and delivering real business benefit. New use-cases of industrial IoT are continually emerging, driving new business models and alternative ways of working.
There is little doubt, then, that for manufacturers, industrial IoT has moved on from the initial early hype. It is now delivering and truly transforming the means of production.
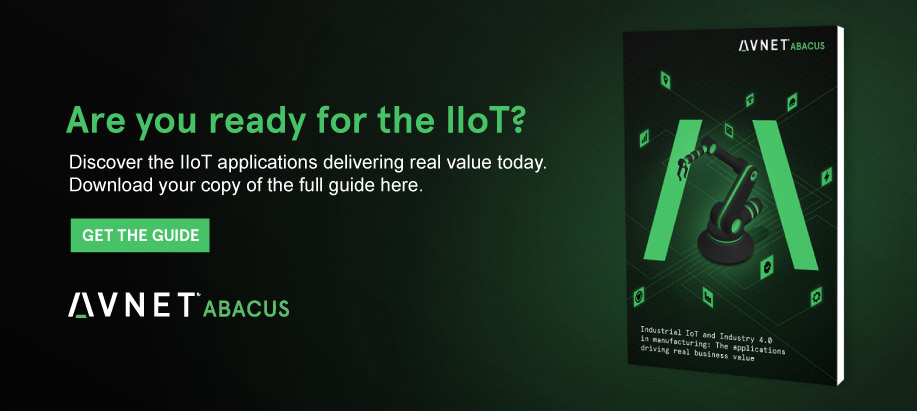