7 game-changing Industrial IoT applications
The conversation around the Internet of Things (IoT) has shifted from the ‘what’ to the ‘how’. Most manufacturers are fully aware that advances in automation, software and connectivity can deliver enormous productivity and efficiency benefits to their operations and are now looking at ways to apply such technology. But such is the all-encompassing nature of industrial IoT that it can be hard to see the wood for the trees.
Here we pinpoint some of the key applications of IoT in manufacturing which use the building blocks of core products such as sensors, wired and wireless connectors, while looking at how such innovation is helping manufacturers to transform the way that they design, build and maintain their products.
Autonomous vehicles: Free-roaming robots move across factory floors
The march of the robots is well underway, says Deloitte, with swarms of autonomous vehicles having found their way on to factory floors as a means of increasing the speed and accuracy of routine operations. Powered by the Internet of Things, these free-roaming robots can be coordinated to a greater extent than ever before, enabling them to perform automated tasks in a controllable and predictable manner, and with minimum human oversight. This gives them the potential to improve operations inside manufacturing plants, particularly in areas such as component handling and transportation, offering opportunities to increase productivity, reduce risk, decrease cost, and improve data collection. This frees up workers to focus their attention on higher-value activities such as production and assembly.
Historically, automated guided vehicles and conveyors have been installed as a means of moving materials and parts around factories. However, most of these systems have depended on pre-set routes that offer no deviation.
Now with the convergence of technologies such as robotics, sensors, 3D cameras, 5G connectivity, software and artificial intelligence, robots are capable of navigating their way safely around factory floors. Some forward-looking manufacturers are ahead of the curve in adopting such systems. In Italy, for example, automotive systems manufacturer Faurecia is using autonomous vehicles from Mobile Industrial Robots to increase the efficiency of its logistics. The organisations have worked together to reorganise Faurecia’s factory layouts to allow robots to navigate their routes using their internal maps. Workers interact with the robots via smartphone, tablet or personal computer interfaces, instructing them of their duties with a push of a button.
Machine utilisation: Making the most of industrial assets
No manufacturer wants to invest in expensive capital equipment, only to see it underused and not earning its keep. That’s why IoT architecture has emerged as a popular and powerful means of monitoring machine utilisation – sending valuable performance data to operators via dashboards to let them know what machinery is working most effectively in comparison to other equipment. These platforms can act as a key driver in improving factory floor production, primarily through the elimination of bottlenecks due to under-performing assets. They can also be used to compare the performance of machines across one or many sites.
Recently, MachineMetrics has been working with Fastenal, the Minnesota-based manufacturer of fasteners and tools, to apply an IoT platform that monitors factory floor production. The software can connect to any modern CNC machine by coupling the MachineMetrics Edge to the Ethernet port of the control, while older machines can share data directly to the cloud via the digital and analogue IO module.
In the Fastenal case, the software gave insight into machine utilisation by the hour, shift, day, week, and month to uncover opportunities to make efficiency improvements. This delivered an 11% increase in machine utilisation in the first three months, says MachineMetrics, which translated to a boost in production of 100 hours, and 150,000 more parts produced.
Operator productivity: Connected tools eliminate human error
A small to medium-sized manufacturing plant might contain hundreds of operator tools, in various shapes and sizes, which are used for a multitude of functions. For a large factory, that number could rise to thousands. Now imagine if all of those hammers, drills, torque wrenches and shears could always be located in an instant, and that they could never be erroneously used outside of a specific set of operational parameters. That’s the promise of IoT-enabled connected tooling, delivering enormous improvements in operator productivity.
Airbus and Bosch have led the way in this area, with the Factory of the Future initiative using connected drilling, measuring and tightening tools. These processes, in aerospace plants, can take place over several work cells and can be performed by different operators. So, says Airbus, there is huge potential for improving these processes by making hand tools more intelligent.
Other manufacturing companies have followed suit. Workers at GE Aviation have, for example, been combining WiFi-enabled torque wrenches with mixed reality headsets to ensure that bolts are tightened most optimally. It is all about improving operator productivity, boosting product quality and eliminate costly re-works.
Power management: Building automation lowers energy costs
Manufacturing, by its very nature, requires a lot of energy, and that in turn can account for a large percentage of operating costs. That’s why factory owners and managers are increasingly turning to IoT-based building management systems to connect sensors, actuators, controllers and other equipment over one IP backbone, enabling the monitoring of energy usage, lighting, HVAC and fire safety systems. This data can also be combined with information from broader datasets such as weather forecasting and financial information - such as the price of electricity and other utilities - to give a far more rounded view of building management. This type of architecture is finding increasing adoption in manufacturing environments, to make buildings smarter, more sustainable and more efficient.
BAE Systems has, for example, worked with Schneider to install its Ecostruxure building management systems platform at one of its production facilities in the UK.
In this particular case, the Ecostruxure platform is being used to monitor HVAC in the warehouse and office areas, along with other equipment including destratification fans, heat recovery units and electric panel heaters. In terms of system configuration, two panels were built by systems integrator Aimteq for the offices and warehouse containing Schneider SmartX AS-P controllers and I/O modules, as well as intuitive touchscreen tablet displays.
Quality control: Vision systems deliver perfect products, time and again
Faster and more flexible production lines might be the key to meeting customer demand, but there can also be a negative impact on quality control if monitoring isn’t up to scratch. These days, as plants look to automation to replace tasks such as manual inspection, new technology is being used to ensure there is no deviation from quality parameters. Increasingly, the function of replacing the human eye has been performed by IoT-enabled high-pixel camera vision systems in combination with other devices such as acoustic sensors, along with high-performance image processing software. These can be used to identify defects such as size, shape or finish, and to check the accuracy and readability of labels, barcodes or QR codes. This information can then be looped back to earlier stages in the production line allowing production managers to identify and classify the root cause of the problem before rectification action can be taken. Over time, artificial intelligence can be applied to learn from feedback and continuously refine and improve the production process.
This type of vision system is being used across manufacturing to monitor the quality of a wide range of products including electronic devices, consumer goods and metal finished parts. For example, the automotive component supplier Getrag has been using a vision system to inspect teeth and clutch body parts, supplying engineers with real-time data on non-conforming parts, and trends emerging from the manufacturing process. The aim is to improve product quality, reduce costly re-work and enhance brand reputation.
Smart logistics: Keeping track of assets in real-time
 |
The benefits of IoT for manufacturers don’t end once products have reached despatch. Indeed, the delivery and logistics function has become one of the primary beneficiaries of digitalisation, with asset-tracking sensors able to provide real-time information on asset location, the surrounding temperature, humidity and motion. These smart logistics systems now benefit from a wide range of connectivity options delivered through low-power, wide-area cellular and noncellular technologies such as LoRa and Narrowband IoT. These networks stream sensor data to the cloud safely and seamlessly, offering a breadth of performance capabilities around latency, data rates and operational range, depending on what is required.
The latest supply chain logistics software means manufacturers can track the movement of their assets via easy-to-read dashboards on devices such as laptops and smartphones, giving managers a complete view of the outbound logistics function.
Manufacturing is expected to be one of the leading industries adopting asset tracking, with the food and beverage sector in particular keen to use it to move perishable goods quicker and more efficiently, and with less damage.
Recently, a joint venture between Hoopo and Polymer Logistics delivered full IoT tracking of pallets and containers using LoRa, meaning it can locate assets without the need for GPS. This maintains the device’s low-power consumption and enables extended battery life while providing data on assets in real-time.
Wearables: Ensuring worker safety at all times
Wearable technology might be closely associated with the consumer sector through the use of fitness monitors, but it is also delivering enormous benefit in industrial environments. In manufacturing, for instance, wearables are increasingly being used to ensure worker safety, with body-worn connected sensors being used to monitor environmental conditions and to provide insight into vital signs such as temperature, pulse and respiration rate.
 |
By embedding personal protective equipment with sensors or radio-frequency identification technology, they become edge devices in the Industrial Internet of Things, collecting and transmitting data to provide insight.
These connected worker platforms aim to more effectively manage worker safety, especially in manufacturing plants which have employees perform tasks alone or handle potentially hazardous substances. It also acts as a means of lowering an organisation’s compliance and administrative costs. Meanwhile, wearables are also being used within manufacturing for ergonomic reasons, to reduce the toll that physical activities take on its workers’ bodies.
The German carmaker Audi is using has been using exoskeleton ergonomic aids in its press shops to provide support for workers when they are lifting and carrying heavy materials. The exoskeletons also allow workers to assume a sitting position when required.
These capabilities have been shown to reduce the strain on the back by 20 to 30 per cent and to promote a healthier posture over the long-term. Increasingly, such devices are being IoT-enabled, allowing occupational health experts to utilise more accurate data for ergonomic purposes, with the right regulatory agreements.
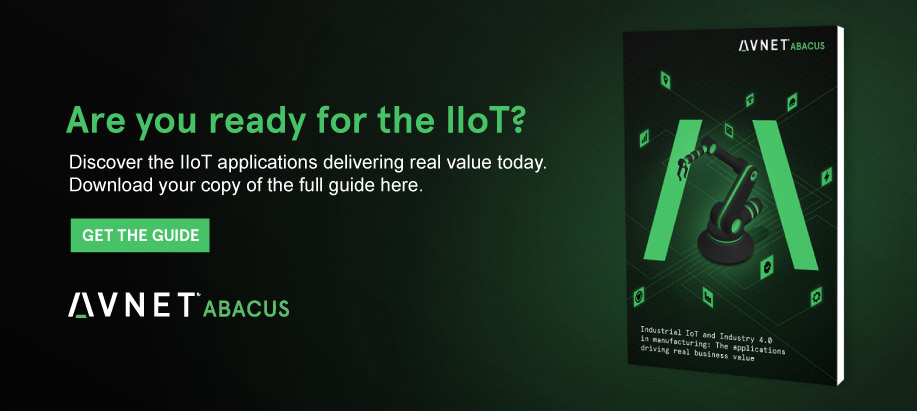