Four industry 4.0 trends transforming manufacturing, now and in the future
The Industrial Internet of Things is driving the intelligent connectivity of devices across manufacturing. Through the combination of sensor data, machine communications and automation systems, IIoT is providing a digital backbone for the emergence of Industry 4.0, the broader set of operating principles that are set to deliver the smarter factories of the future. Here we outline four key technology trends that have the potential to change the face of industrial production.
Cobots will augment people on the production line
Not too long ago, robots in factories knew their place – behind safety cages, well out of harm’s way. But that has changed. Now, a new breed of collaborative robots (cobots), comprising a suite of positional sensors along with connectivity, has been developed to work safely alongside humans, increasing the flexibility of production line and boosting productivity.
Indeed, the market for cobots is growing at an astonishing rate, with research by Markets and Markets estimating that it will increase from $900 million to $12 billion by 2025, at a compounded annual growth rate of 50.31% during the forecast period.
Importantly, the affordable nature of cobots – driven in part by their lower payload capacity than traditional robotic arms – means that small companies are expected to become significant adopters of the technology.
These organisations, with a firm eye on Industry 4.0 techniques, are keen to embrace cobots as a means of introducing new production methods, helping workers to increase their productivity.
So far, it has been the automotive manufacturing sector that has been the most active adopters of cobots, using them for tasks such as pick and place, machine tending and materials handling. Continental, for example, has started using cobots to automate the handling of PCB boards, relieving production line workers of the manual task of moving components from one station to the next. This has allowed the workers to concentrate on other more skilled tasks that contribute to improving production. This simple application of cobots has seen Continental slash changeover times to 20 minutes, a reduction of 50% when compared to performing the task manually.
So, the march of the cobots is underway, and the future will see a broader range of use-cases. While automotive has set the pace, expect other sectors such as electronics, food and beverage, and metals and machining to follow suit.
3D printing is making production faster and easier
For many years, 3D printing was viewed as an exciting technology looking for an application. Yes, the ability to produce parts additively rather than subtractively was a novel idea and promised significant design advantages, but limitations in machine reliability and quality meant many manufacturers viewed the technique quizzically from afar.
That is no longer the case. Rapid advances in 3D printing mean the latest generation of machines can be used to produce prototype and production parts, quickly and accurately, in both metals and polymers. That means 3D printing is finding an increasing role on the factory floor, helping manufacturers to become faster and more flexible by eliminating the need for new moulds and tooling. This is delivering exciting new techniques such as mass customisation
Some companies are already ahead of the game. Volkswagen, for instance, has been using additive technology to build personalisation into its range of luxury vehicles, producing individualised gear knobs. The company is also thought to be looking at customised tailgates, while other automotive firms are also embracing the technique for different applications.
The opportunity in other sectors is equally compelling. Sports companies are looking at 3D printing-enabled mass customisation as a means of adding different elements to their latest designs of trainers and clothing, while consumer electronics makers are using it to experiment with delivering a choice of colour, size of hard drive and keyboard language.
Of course, mass customisation is just one application of 3D printing in manufacturing. It can also be used to build production parts with optimised internal design, such as cooling channels, which couldn’t be produced through subtraction.
Such flexibility means 3D printing is really finding its footing within manufacturing, being used as a primary tool in the pursuit of Industry 4.0. According to the Wohlers Report, the forecast for 2020 is $15.8 billion for all 3D printing products and services worldwide, with manufacturing expected to account for a significant portion of those sales.
As technology continues to improve, and new use-cases are found, 3D printing will never again be viewed as a technological oddity – it will be central to the future of manufacturing.
Factories-in-a-box bring automation on demand
Manufacturing is an expensive business, with plenty of upfront costs. Buildings, equipment and skilled staff all act as a drain on resources, preventing many innovative smaller companies from putting their good ideas into production.
But what if things could be done more flexibly and cost-effectively, and with less capital-intensive expenditure? That’s the promise of the factory-in-a-box, which is ushering in the era of automation-as-a-service.
So, what’s in the box? That depends on the specific configuration, but it usually comprises robotics and additive manufacturing alongside augmented reality/virtual reality, powered by full over-the-air connectivity through 4G/5G networks
The technologies, which can be packed in a container, transported and brought back into service in a matter of hours, means manufacturers can take advantage of Industry 4.0 solutions in the most agile way possible.
The concept is being developed by organisations such as Nokia, which teamed up with around a dozen other companies in the electronics sector to launch a factory-in-a-box version 2.0 at the Hannover Messe earlier this year. The Nokia consortium thinks that the concept delivers several critical advantages to the manufacturing industry. This includes enabling building for ‘country of origin’ requirements, delivering faster prototype production for shorter time-to-market, and providing assistance with disaster recovery and business continuity.
Meanwhile, experts at the Manufacturing Technology Centre in Coventry, UK, have also built a factory-in-a-box demonstrator to guide businesses through the process of adopting smart manufacturing technologies and processes. The demonstrator - which is part of the £60 million Innovate UK funded Energy Research Accelerator programme – is being used to show companies how industrial digital technologies can speed up their route to market and result in new business models.
Ultimately, this kind of automation-on-demand will democratise new technology – making the benefits available to all.
VR/AR build partnerships between man and machine
The merging of the digital and the physical worlds means manufacturing workers are now more likely to be armed with tablets and headsets than paper-based manuals and drawings. With digital twins being used to create interactive replicas of industrial assets, employees can use innovative methods of making sense of data in real-time, improving their productivity.
Both virtual and augmented reality are already delivering tangible benefits. Virtual reality – characterised by a computer-generated experience taking place within a simulated environment, usually via a headset, completely shutting out the physical world – has found application as a means of providing safe and structured training for manufacturing workers. It has also been used by several large organisations as a means of designing virtual factory layouts, before construction of the real thing.
AR provides other advantages. By building digital elements such as graphics and data into a live real-world view, often by using the camera on a tablet or headset, AR has emerged as a key enabler of more interactive maintenance in manufacturing. With 3D animations and other instructions through head-mounted displays, workers can go about their tasks in a more informed manner, reducing human errors and execution times.
Examples are increasing at a rapid pace. Service engineers at Tetra Pak, for example, work alongside customers using AR to reduce machine downtime. With the use of line-of-sight headsets, experts can be ‘beamed in’ in real-time to solve any maintenance problems, no matter where they are in the world.
Clearly, the market for AR/VR is already well established – but there’s plenty of scope for future growth. Research by the International Data Corporation (IDC) predicts that the market will be worth 16.8 billion U.S. dollars in 2019, growing to $160 billion by 2023. Expect the technology to become ubiquitous, especially as AR/VR become cheaper and more accessible through the emergence of new business models such as mixed reality-as-a-service.
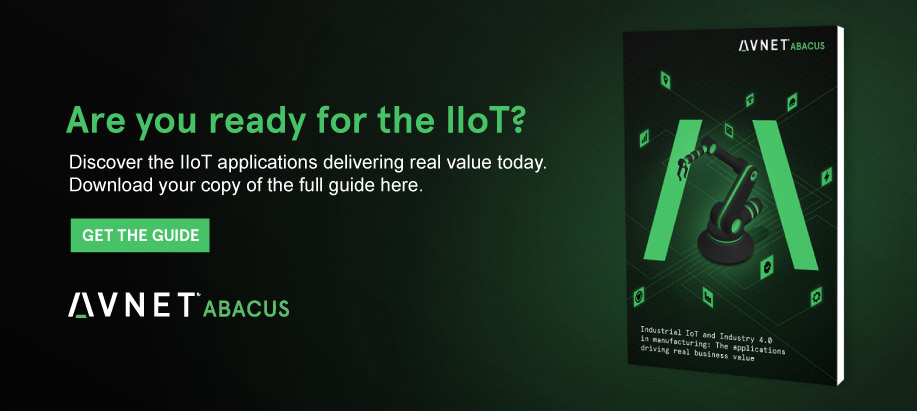