Industry 4.0 in manufacturing: 26 applications driving real business value
Manufacturing is entering the fourth industrial revolution. Digitalisation - powered by the use of sensors, software, connectivity and big data analytics - is resulting in leaner and more efficient factories and driving the introduction of flexible new business models.
It’s been quite the journey to get to where we are today. The first industrial revolution, kick-started by the invention of water and steam-powered engines, led to the first organised means of production. The second was characterised by the invention of electricity, resulting in the first moving assembly lines. The third industrial revolution was made possible by the advent of the computer. And now we stand ready for Industry 4.0, with technologies such as sensors, connectivity, communication, data and artificial intelligence-powered analytics combining to create the factories of the future.
But what does this all mean in reality?
How is Industry 4.0 actually changing the face of manufacturing as we know it?
8 business value drivers and 26 levers
A good starting point in all of this is the McKinsey digital compass, which identifies eight business value drivers. These comprise of:
- Resource/process
- Asset utilisation
- Labour
- Inventories
- Quality
- Supply/demand match
- Time to market
- Service/after sales
Within these eight drivers come a total of 26 business levers – the Industry 4.0 applications that are changing the way that manufactured goods are planned, designed, made and repaired. Here we take a look in turn at each of these business applications, explaining what they are and how they are delivering benefit to the manufacturing industry.
The resource/process levers
1. Smart energy consumption
Automated building management systems connect sensors, actuators, controllers and other equipment over one IP backbone, enabling the monitoring of energy usage from machinery, lighting, HVAC and fire safety detectors systems. This information can be combined with broader datasets such as weather forecasting and real-time pricing of electricity and other utilities to give a more centralised and informed view of building performance.
This kind of automated building management system has been installed at a Schlumberger factory in France, monitoring air quality, temperature and lighting. The aim, ultimately, is to use energy more efficiently and to drive down costs.
2. Intelligent lots
Industry 4.0 is proving to be a key driver of improved process effectiveness inside manufacturing plants. Digitisation of the supply chain through methods such as intelligent lots – characterised by smart information storage in products and pallets – is a good example of that, encouraging the adoption of just-in-time manufacturing. Through use of technologies such as RFID tags and sensors, with cellular 3G, LoRa WAN, NB IoT, Wi-Fi and Bluetooth connectivity, items such as containers, pallets and roll cages can be tracked and monitored prior to delivery and once stored inside the warehouse. This data can reveal information on location, inventory and temperature, and can act as the foundation for advanced technologies such as automated picking.
This kind of technology has been used to good effect by NGK Ceramics, which makes parts for catalytic converters at a 500,000 sq. ft plant in the US. The company is using IoT-enabled tracking to help workers monitor the pallets across the entire facility, while always maintaining an always up-to-date inventory.
3. Real-time yield optimisation
The networking of industrial assets through sensors, software and wired and wireless connectivity can be used to provide an accurate snapshot of equipment performance at any point in time. With the addition of machine learning, this evaluation can be progressed to become real-time yield optimisation in manufacturing environments – with outputs continually re-calibrated to achieve optimal performance, depending on a host of variable factors. This ensures that industrial assets are always working to maximum efficiency.
One of the first examples of real-time yield optimisation was reported by engineering giant ABB, which has used the technology for the control and optimisation of a cement kiln in Australia, mimicking the actions of an “ideal” cement plant operator and implementing automatic adjustments to achieve targets. This has boosted kiln stability and helped deliver a reduction in energy used per ton of clinker produced.
The asset utilisation levers
4. Routing flexibility
Modern manufacturing requires new levels of plant adaptability as companies look to become more responsive to changing customer needs. This has resulted in the increasing use of flexible manufacturing systems, which use IoT-enabled technologies to help companies become more reactive. Routing flexibility, for instance, represents the ability of manufacturers to cope with factors such as equipment breakdowns to enable continuation of production for any given component. This could be achieved in several ways, such as manufacturing a particular part through different routes or by continuing operation on more than one machine. Routing flexibility is performed by employing hierarchical models of job shop activity, allowing dynamic simulation of production activities. This flexible approach increases factory adaptability by maximising asset utilisation and increasing uptime.
5. Machine flexibility
As the implementation of Industry 4.0 methodologies result in manufacturing becoming a more decentralised, autonomous process, so machine flexibility is likely to become an exciting area of development. This trend will be driven by the use of standard interfaces and intelligent infrastructure that enables a far more modular approach to industrial networking and automation, with ‘plug and produce’ modules encouraging the swift reconfiguration of production line facilities. That might mean quick-fit data/communication cables for robotic arms, or high-level sensors that interface with Ethernet – eliminating the need for a standard I/O module. Such machine flexibility drives more dynamic manufacturing lines, with much faster and intuitive maintenance.
6. Remote monitoring and control
Manufacturing plants are complex ecosystems with hundreds or even thousands of pieces of equipment working seamlessly together for an end result. When you add in the fact that some production plants don’t stand in isolation – being perhaps part of a global network of facilities – then the importance of having visibility of all operational processes becomes clear. IoT-enabled architecture offers this insight, in real-time, from anywhere in the world. Engineers can plug into networked systems through tablet, laptop or mobile dashboards, allowing them to drill into the performance of individual assets.
This remote monitoring and control can be used as a primary means of identifying and eliminating bottlenecks and reducing waste. US automotive component manufacturer Varoc has been using such an approach to monitoring machine health, resulting in a 20 per cent increase in overall equipment effectiveness.
7. Predictive maintenance
The combination of sensors and wireless connectivity means industrial equipment of all kinds can be monitored in real-time, with data analytics powered by machine learning then used to identify trends and anomalies. Instead of performing traditional calendar-based maintenance using the periodic examination of equipment, or adopting ‘if it ain’t broke, don’t fix it’ strategies, engineers can track patterns of failure more effectively, spotting any potential problems before they occur.
By unleashing the potential of truly predictive maintenance regimes, manufacturers can reap enormous benefit through the eradication of unplanned downtime and associated costs, particularly when it comes to mission-critical pieces of equipment. Valve and control components manufacturer Gemu has been using such an approach to good effect, monitoring its production processes and detecting and replacing any under-performing components before they fail.
8. Augmented reality for MRO
The days of maintenance professionals referring to well-worn instruction manuals as they repair machinery in manufacturing plants is becoming a thing of the past. These days, workers are just as likely to be equipped with augmented reality headsets – providing them with a wealth of information such as computer-aided data, diagrams and drawings in their line-of-sight as they go about their tasks. Such capability is being driven by rapid advances in image recognition technologies, computing power, wireless connectivity and the Internet of Things.
The benefit of augmented reality-enabled maintenance is clear: immediate access to the right information, delivered in an intuitive way, means employees can perform higher quality work in less time, with reduced errors. Festo, for instance, is trialling Microsoft HoloLens augmented reality headsets glasses to conduct a wide range of maintenance activities at its sites in Europe and the US.
The labour levers
9. Human-robot collaboration
Lightweight, space-saving robots that can operate alongside humans without safety caging are delivering new levels of flexibility within smart factory environments. These collaborative robots, which are fitted with a suite of sophisticated motion, vision and positioning sensors, can perform a host of repetitive and dull jobs, freeing up workers to add value in other areas.
At thyssenkrupp, cobots have been installed at one of its plants producing automotive suspension systems performing roles associated with machine tending, assembly, and product inspection. This has allowed thyssenkrupp to improve efficiency and expand its business during a period of skill shortages.
10. Remote monitoring and control
Cloud-based remote monitoring answers two primary questions. Where are my assets? And how are they doing? That information – accessible in real-time with the information delivered to dashboards on mobile devices – frees up the worker in the manufacturing plant to an enormous extent. Having information on factors such as temperature, pressure, volume, energy consumption, loaded hours and unloaded hours within instant reach, workers can make smarter decisions based on more reliable data, which improves productivity and increases uptime.
11. Digital performance management
Digitalisation provides the opportunity for manufacturers to monitor more than just the performance of machines. Other cost drivers such as materials and manpower can be assessed, and KPIs automated, through digital performance and operations management systems. Such an approach provides a more accurate means of cost allocation across an organisation, and therefore an ability to improve cost calculations and overall financial performance.
12. Automation of knowledge work
We are familiar with robots taking over manual tasks that were previously performed by humans. But what if automated technologies could also start performing some aspects of ‘knowledge work’ currently performed by employees? The phrase was first adopted by McKinsey to mean the use of computers to perform tasks that rely on ‘complex analyses, subtle judgments, and creative problem solving’.
A report from the McKinsey Global Institute, suggested automation of knowledge work will be high up in its list of top ten disruptive technologies by 2025. This automation of business processes could have a big impact on manufacturing in areas such as procurement, marketing and customers’ services – not necessarily replacing humans, but complementing them in certain roles.
The inventory levers
13. Batch size
Industry 4.0 is driving faster and more flexible production, with increasing levels of customisation. Taken to an extreme, seamless production systems should be capable of switching out of serial processes to manufacture a single part just as quickly and efficiently as they can make multiple parts. This ability to produce ‘batch size 1’ provides firms with the opportunity to achieve new levels of mass customisation – effectively ‘making to order’ for individual customers.
Automation is key to batch size 1 methodologies. At bespoke beauty product manufacturer AlpStories, for example, robotic arms are used to start making its customers’ ‘beauty boxes’ as soon as an order is received. The dual-arm Motoman CSDA10F robots use multifunctional tools and grippers to pick and pack, and the arms can be quickly re-programmed to learn new workflows. It is this type of approach to batch size 1 – the ability to produce single units flexibly and economically – which will drive new approaches to inventories, based on more dynamic demand forecasting.
14. Real-time supply-chain optimisation
Supply chains in the era of Industry 4.0 are faster, more flexible, and more transparent. The combination of ubiquitous sensors and connectivity, in combination with big data analytics, means manufacturers can have total visibility of their incoming components, knowing the exact location and condition of each shipment. Automated handling ensures goods are picked and placed in exactly the right spot in the warehouse, while networked machines give feedback on real-time production rates. This creates an optimised loop back to the purchasing department.
Real-time supply-chain optimisation can deliver some marked benefits. Hitachi, for example, has embarked on a complete optimisation of inventory and supply chain across its production facilities in Asia, therefore reducing goods in stock, cutting logistics costs, and improving logistics flexibility.
15. In-situ 3D printing
The performance of 3D printing equipment has improved dramatically in recent years, with the latest machines able to produce polymer and metal components in a reliable and repeatable manner. This has led to 3D printers escaping the confines of traditional prototyping roles to provide a flexible means of making spares or replacement parts. In this way, manufacturers can reduce the need for warehousing in favour of on-demand production of some components in or near its own facility, providing greater supply-chain resilience.
Some big players have already recognised the value of in-situ printing: Siemens Mobility, for example, has established a digital machining centre at its train manufacturing plant in Germany, making 3D print replacement parts and tools on demand.
The quality levers
16. Digital quality management
We’ve discussed Industry 4.0, but what about Quality 4.0? It represents the use of big data analytics to deliver a shift in the way that quality is measured.
It’s no longer good enough just to measure quality by looking at the integrity of products – digital quality management provides an opportunity to integrate quality throughout the value chain, from supply through to delivery.
According to Sparta Systems’ 3 Steps to Quality in the Cloud, a move away from old-style quality measurement based on paper records towards adoption of a digital quality management system in the cloud can result in lower costs, better compliance and an improved user experience.
A case study published by quality management software supplier Cebos shows how it has helped components supplier Vishay Dale get better control of its internal documentation, creating a system that significantly minimised time and effort required to execute engineering challenges. This has supported product quality and increased operational efficiency.
17. Advanced process control
Modern facilities comprise an intricate network of production processes controlling a multitude of factors such as feedstock, temperature and other operational targets. Increasingly, the application of advanced process control is being used to provide a common platform for procedure optimisation through activities such as data collection and analysis and dynamic modelling, with a view to improving quality, increasing throughput and reducing energy use.
The software can be used to oversee a broad range of variables such as feed rates, inlet air temperatures and powder moisture, making minute adjustments to improve product quality and boost plant performance. Advanced process control is finding particular application in the food and beverage manufacturing sector, with an Aveva case study showing how spray dryer optimisation for one particular client resulted in a 10 per cent increase in throughput and an 8 per cent reduction in specific energy consumption, with zero product quality violations.
18. Statistical process control
Numbers matter in manufacturing, with a slew of statistics available to provide insight into quality during the production process. This data is captured in real time, and then plotted on graphs with predetermined control limits based on the capability of the process. Variations that occur outside of the parameters provide insight into faltering operations, which can have an impact on quality.
This type of statistical process control has been used to good effect at Nestle Waters, the bottled water manufacturer, which has used an InfinityQS statistical process control software to replace a cumbersome paper-based system to collect and analyse data, providing real-time visibility across 26 factories. By tracking trends in data, the company has been able to make more accurate decisions about process improvements in areas such as cap torque, providing more consistent levels of product quality.
The supply/demand match levers
19. Data-driven design to value
Ubiquitous sensors are changing the way that discrete manufacturers bring products to market. By connecting sensors to prototypes, and using the data created from testing to get a better idea of real-life operational scenarios, manufacturers are able to develop better-performing products that are more closely aligned to their customers’ needs. This approach, known as data-driven design to value, doesn’t stop with prototypes, though. Sensors fitted to products out in the field continue to provide operational insight, allowing further product refinement.
PTC is a leader here, with a case study outlining the design requirements of a tractor. Instead of making assumptions about factors such as what the maximum load the tractor’s bucket should support, data-driven design to value is applied to ensure the product isn’t over-engineered (adding time and cost) or under-engineered (decreasing performance and customer satisfaction).
20. Data-driven demand prediction
External factors can have an enormous impact on manufacturers. Sudden changes in consumer spending can, for example, drive a hole through the most careful forecasting and decision making. Enter data-driven demand prediction – cloud-based predictive economic intelligence software that provides a 360-degree view of future demand. In manufacturing environments, the software uses global data, analytics and expert services to identify future threats or opportunities to business performance across finance, sales, marketing and operations.
Research by Prevedere suggests that data-driven demand prediction can provide accurate insight into future activities, being used to make changes in production levels or to validate expansion plans, with manufacturing companies improving demand forecast accuracy by more than 20%.
The time to market levers
21. Rapid experimentation and simulation
Software has long since been used to increase the speed of experimentation. Now, though, advanced hardware such as 3D printers are being used to further accelerate time-to-market. The additive process is particularly suited to rapid creation of prototype parts, with the findings looped back into the design and simulation process for further refinement. Previously, manufacturers would have needed to pass each design iteration to its production department, or outsourced the work, causing delay.
According to Sculpteo’s 4th edition of The State of 3D Printing report, accelerating product development is the highest priority for companies that are relying on 3D printing. Prototyping (55%) production (43%) and proof of concept models (41%) are the three most popular 3D printing uses today.
22. Concurrent engineering
The parallelisation of tasks – often referred to as concurrent engineering – can quicken the product development process. But structuring those parallel processes can prove difficult if collaborative tools aren’t in place as part of wider Industry 4.0 strategies.
This is where the latest software from organisations such as PTC aid the concurrent process, by providing a ‘skeleton’ planned out by the lead designer to ensure that everyone has access to the information they need and have a common basis from which to work.
Engineers can then go about concurrent tasks without fear of accidentally overwriting one another’s files. Once the primary design is in place, the individual subassemblies will adapt. The motorcycle manufacturer KTM has been using this approach on its KTM 690 DUKE bike which was developed in just 22 months from first concept to start of production, a 15% reduction in time-to-market compared to the previous generation.
23. Customer co-creation/open innovation
Industry 4.0 is creating a more collaborative environment in manufacturing, which is increasing levels of customer co-creation and open innovation. Through this, the design process can be shared by other parties such as customers or suppliers, or students at a local university. Such an approach builds transparency and trust, encourages lateral thinking and often results in more customer-centric products. It can also reduce time-to-market.
The French automotive supplier Valeo has been particularly active in this area through its Innovation Challenge, which uses an innovation contest to generate ideas. The company has chosen students from all over the world as its target group. The competition brings the company into contact with high potentials from all over the world – with the latest contest involving 1627 teams from 748 universities from 80 countries, competing for the two prizes of $100,000 each.
The service/aftersales levers
24. Predictive maintenance
Digitalisation is transforming the servicing of industrial equipment. Under some after-care packages, sensors, software and connectivity enable the manufacturer of machines such as drives and motors to assess the performance of their products in-situ, helping the customer to avoid downtime by predicting problems before they occur.
This IoT-enabled architecture is also leading to the creation of new business models based on servitisation, where the end-user effectively leases a service or a solution rather than buying a machine, therefore avoiding large upfront capital cost. This service is based on KPIs such as available uptime, giving the manufacturer clearer visibility of maintenance schedules. The seller of the service, meanwhile, receives predictable revenues.
25. Remote maintenance
Traditionally, if a machine failed at a manufacturing plant, the in-house maintenance team was charged with carrying out the repair or calling the OEM to book a service engineer. Now remote monitoring of in-situ equipment can be extended to remote maintenance, with experts from the OEM able to perform some tasks without the need for a physical presence.
For example, software updates and rectifications can be securely installed over the air, bringing equipment quickly back online. Remote maintenance can also be delivered through augmented reality headsets, with maintenance workers at the plant receiving repair instructions in their line-of-sight. For example, Plex Systems is using remote maintenance with mixed reality to bring customers’ equipment back into operation, supporting the inhouse maintenance team.
26. Virtually guided self-service
The application of artificial intelligence within manufacturing isn’t restricted to the production function – it’s also making its mark on customer service and after care. Virtually guided self-service denotes the use of virtual agents on company websites, helping customers to resolve problems.
According to Gartner, a quarter of digital workers will use a virtual employee assistant (VEA) on a daily basis by 2021. This will be up from less than 2 percent in 2019. While virtual agents have been used in sectors such as insurance and financial services, Gartner suggests they will find their way into manufacturing.
Nokia's Multi-purpose Intuitive Knowledge Assistant (MIKA), helps engineers find answers as they perform complex tasks or diagnose problems on their network. Ultimately, these virtually guided self-service assistants provide OEMs with an additional communication channel, while helping to drive down costs.
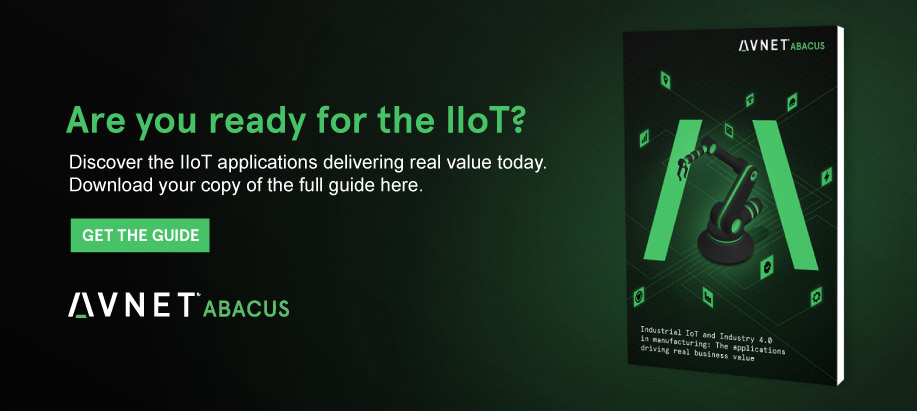