LED drivers: constant voltage vs. constant current
LEDs are now the default method of lighting offices, factories, and public spaces. Their long life, low energy and compact attributes have proved to be extremely popular for a diverse range of lighting requirements. The technology itself has advanced significantly, with heat dissipation innovations crucial to its use in lighting large areas.
LED drivers, used to power LED-based lighting installations, are available in two different types: constant voltage and constant current. When choosing an LED driver, it helps to understand the differences between the two driver types.
But before we get into the detail of the drivers, it will help to look more closely at the characteristics of an LED.
Characteristics of an LED
LEDs are semiconductors where the junctions produce light when powered by a DC voltage. Like all semiconductors, they only conduct electricity in one direction and, consequently, the connecting wires indicate the polarity. Light comes from the LED when electrical current flows through it from the anode (+) to the cathode (-).
The amount of light produced is proportional to the applied voltage and current. If too much voltage is applied or too much current flows, the LED emitter will be permanently damaged. When the LED is conducting and producing light, the current flow is termed the forward current, and the applied voltage, the forward voltage.
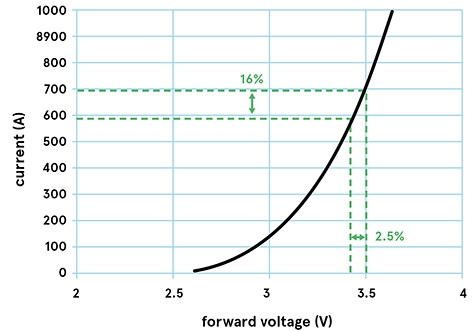
Figure 1: Forward voltage against the forward current |
One of the principal non-linear characteristics of an LED is that relatively small changes in forward voltage can result in more significant changes in the forward current, as shown in Figure 1.
More forward current emits more light from the LED's junction. The forward current produces a heating effect in the LED, which, in turn, can result in more current flow. This unwanted attribute of an LED emitter creates a thermal runaway condition, driving more current and further increasing the temperature. If this is not stopped, it causes the LED junction to fail.
From the reliability standpoint, the cooler an LED can operate, the longer it will last, so there is an optimum balance between light output and forward drive current.
The junction temperature of an LED during operation can be very high, typically up to 200°C. Thermal management, through the use of heatsinks, is crucial to securing a long service life. Managing the current flow through an LED is also a critical factor.
What is a constant voltage LED driver?
A constant voltage LED driver delivers a tightly regulated output voltage across all load conditions to the LED light(s). Typically, these units are mains-powered AC-DC power supplies specifically designed for LED lighting applications.
Constant voltage LED drivers will continue to supply the output voltage up to a maximum current limit, above which the overcurrent protection (OCP) will turn off the DC supply.
The available range of output voltages depends on the type of application but typically includes the popular nominal output voltages of 12 VDC and 24 VDC for small single LED installations. However, for large scale LED installations, the trend to gather multiple LEDs into multiple series-connected strings pushes the drive voltage requirement into the hundreds of volts.
What is a constant current LED driver?
As the name suggests, a constant current LED driver supplies a carefully controlled current flow across a given range of output voltages. Such LED driver power supplies quote the nominal continuous current output in mA or A, and the voltage range over which it operates. The driver varies the output voltage to maintain the current at the prescribed value.
Constant current LED drivers are particularly well suited for high power lighting applications. They maintain optimal and consistent light output, particularly for strings of LEDs, while preventing thermal runaway conditions from occurring.
Controlling an LED driver
Most LED drivers provide some degree of programmability and control. Some basic features include being able to control or sequence the output to LED lights and strings using a microcontroller-based system.
More sophisticated features include the ability to program or configure the LED driver's current and voltage outputs, and set the over current, over voltage protection limits.
The requirement to control large-scale LED lighting installations has led to the development of lighting control standards. The most popular of these communications protocol standards used in the industry are the digital addressable lighting interface (DALI) and the digital multiplex (DMX).
The causes of flicker in LED lighting installations
The ability to control the light output, such as dimming, is also a popular control requirement although it needs careful attention due to the potential side effect of flicker.
Most LED drivers use a pulse width modulated (PWM) technique to control the LED drive voltage and current. PWM operates by rapidly switching the output voltage at a high frequency. The width of the pulse determines how long the LED is on within a given duration, thereby controlling the duty cycle. This switching reduces the light output, resulting in a dimming effect.
However, LEDs can, unlike incandescent bulbs, respond instantaneously to changes in drive voltage. At high dimming levels, and depending on the switching frequency, the human eye can detect the switching and interpret it as flicker.
Flicker is an annoyance and can induce headaches, migraines and cause discomfort for many people. Flicker can also occur due to poorly designed LED drivers.
LED drivers utilise switched-mode power supply concepts to convert a mains AC voltage to the required DC LED drive voltage. The power conversion topology can leave small regular low-frequency voltage variations on the DC output.
The voltage variations, termed ripple, can be up to 200 mV, and are typically filtered and smoothed out in well-designed LED drivers. However, such a ripple voltage can represent a significant enough variation to induce flicker in the LED light output.
Safety certifications
LED drivers, LED emitter modules, and LED luminaires need to conform to internationally recognised safety standards.
From the LED driver perspective, the rules include electrical safety and electromagnetic compatibility (EMC). IEC 61347-1-13 covers all aspects of electrical safety, including isolation of the lethal AC mains voltage from appearing on the DC output, resistance to moisture, and insulation to prevent users from coming into contact with high voltages.
EMC is an increasingly important aspect of most electronics-based designs today, and since all LED drivers use switching topologies for power conversion and dimming, they can generate electromagnetic interference. The limits of EMC are covered by CISPR 15, while electromagnetic immunity standards include IEC 61547 and IEC 61000.
In our world of high energy prices, the energy efficiency of the LED driver is an important consideration. The European Eco-Design Directive stipulates minimum levels of energy efficiency the driver needs to comply with under full load, low load, and in standby conditions.

Figure 2: The output current and voltage characteristics of the Meanwell XLG-75-H |
Constant power LED drivers
A recent innovation in LED drivers is the constant power LED driver that controls the output voltage and current to deliver constant power to the LED. Combining the ability to control the voltage and the current allows driving the LED for the optimum amount of light output and junction temperature so that it operates at its peak capability.
Above all, constant power LED drivers provide lighting engineers with a more flexible and easily configurable LED drive capability to suit a diverse range of applications. Rather than having to specify either a constant current or a constant voltage driver, the lighting systems designer has a more versatile driver capability that can help simplify lighting implementations.
An example of this is the Meanwell XLG-75-H, which illustrates the range of drive current and voltage possible to maintain a constant power envelope (see Figure 2).
Selecting which type of LED driver to use
The selection of an LED driver involves several vital criteria, of which LED voltage, current, and the type of application are the primary considerations.
For simple, small LED lighting applications, a constant voltage LED driver is probably all that is required. However, as the number of or the output power of the LEDs increases - mainly where long strings are involved - the need to more carefully manage the drive current warrants the use of a constant current LED driver.
From a practical design perspective, the constant power driver offers the most flexibility. Checking that the selected LED driver conforms to the relevant safety and energy efficiency standards is also an essential step in the selection process.
LED lighting spans many different indoor and outdoor use cases from product display cabinets to motorway lighting and everything in between. LED-based lighting provides an energy efficient, controllable, and reliable means of lighting any environment. Powering the LED requires a well-designed driver that can operate continuously, is dimmable and does not cause flicker. With this in mind, our power specialists can help you find the right solution for your designs. Get in touch to discuss your requirements.