Differential pressure sensors
What are differential pressure sensors?
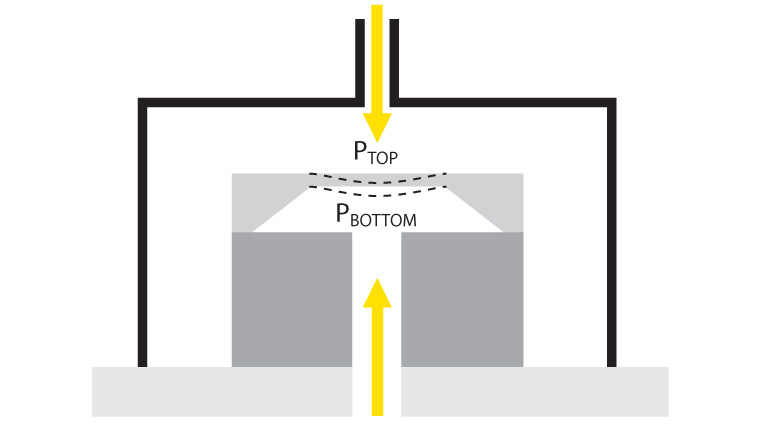
A differential pressure sensor measures the difference in pressure at its two ports |
Sometimes it’s not necessary to know the absolute pressure of a liquid or a gas. Instead, only the difference between two points in the system being monitored need be known. In such situations, you can turn to differential pressure sensors.
The differential pressure sensor will give you a comparative measurement between two points (see diagam right). One example may be before and after a valve in a pipe. If the valve is fully open, the pressure on both sides should be the same. If there’s a difference in the pressure, it could be the valve isn’t fully open or there’s a blockage.
Differential pressure sensors are typically packaged with two ports to which pipes can be attached. The pipes are then connected to the system where the measurement is to be made. Industrial differential sensors may be integrated into a standardised fitting, allowing it to be built into existing pipework.
The measurements made are fully independent of atmospheric pressure, unlike gauge sensors.
How does a differential pressure sensor sense pressure?
Typically, the two pressures to be measured are applied to opposite sides of a single diaphragm. The deflection of the diaphragm, either positive or negative with respect to the resting state, determines the difference in pressure.
Some industrial differential sensors actually use two separate absolute sensors, utilising internal electronics to calculate and provide the difference in pressure to the control system.
If required, a differential pressure measurement can be made using two absolute pressure sensors and software on a control system
Or if necessary, the differential measurement can also be achieved using two absolute pressure sensors then calculating the difference on an industrial control system. This may be the case in situations where two different types of sensors are required due to the medium being measured, such as a liquid and a gas, or the environment of the measurement (see above).

An example circuit for amplifying the signal from a
Wheatstone bridge piezoresistive pressure sensor |
Many of the board-level sensors available utilise piezoresistive sensing elements. The simplest of these use a Wheatstone bridge configuration which requires a signal conditioning circuit to amplify its output (see left).
Circuits like the above diagram apply a constant current to the bridge. The output signal is then amplified and applied to the input of the measurement system. If your application is based upon a microcontroller, the signal could be connected to an ADC input pin. Otherwise, there are many standalone ADCs with digital outputs that could be sourced as an alternative.
The analogue front end (AFE) may also need to allow provision for offset voltage, temperature compensation, and span.
If you’re looking for a simpler solution, many manufacturers provide fully integrated differential sensors. For example, some may include temperature compensation circuitry together with two stages of amplification, enabling it to be simply connected to the ADC input of a microcontroller.
How do I integrate a differential pressure sensor into my circuit?
If you’re developing a microcontroller-based differential pressure measurement system there are a wide range of board-mounting sensors available to choose from. As we’ve already seen, some provide a conditioned and amplified analogue output that can be applied to an ADC input.
Others digitise the signal inside the sensor, allowing them to be connected to a digital serial interface such as I2C or ZACwire.
I2C is a relatively well-known interfacing technology and is even available on some of the smallest 8-bit microcontrollers. Requiring just two wires, one is used for a clock while the second is a bi-directional data line.
Since I2C supports multiple nodes, it’s also important to consider the overall bandwidth of the bus. As more devices are added to the bus, the risk that the pressure sensor cannot be accessed as often as desired increases. Another important consideration is the dimensioning of the pull-up resistors on the bus. The official specification for I2C provides a proper explanation of how to calculate the necessary values.
Can I use an industrial differential pressure sensor in my design?
There’s an obvious attraction to using an industrial pressure sensor over board-level devices. They’re robustly built, housed mostly in a steel casing, and feature a threaded fitting, making them easy to fit to pipes and tanks. Industrial pressure sensors are primarily designed for integration into manufacturing environments, linked to a programmable logic controller (PLC).
Because industrial sensors are used in systems that require high levels of functional safety and robustness, the interfaces they offer can seem a little unusual. Most analogue output sensors provide a voltage output with a wide range (0 – 20 V) or provide their output as a current in the range of 4 – 20 mA. The goal behind such sensor interfaces is to minimise sensitivity to background noise over the long cable lengths employed. Some examples of transmitter type gauge sensor circuitry are shown below.

Example circuits showing how a gauge sensor transmitter may be implemented
Like in other business sectors, industrial sensors are also moving to digital interfaces. This has the advantage that several sensors can all be connected to the same wiring loop, saving on cabling complexity. Some of these interfaces, such as CANopen, can be connected to a microcontroller relatively easily. As long as a CAN interface is available, all that’s needed is a compliant CAN transceiver on the hardware side. In order to implement your software, you'll find a range of software stacks from various embedded software vendors.
What applications are differential pressure sensors used in?
Differential pressure sensors often find a home in industrial environments where a difference in pressure can be used to determine the flow of gases or liquids. This can include effluent treatment plants, offshore and subsea gas and oil processing, and remote heating systems utilising heated water or steam.
They also find their way into the sprinkler systems installed for fire protection.
If it’s necessary to measure the volume of liquid in a closed vessel, a differential pressure transmitter can also be used. As long as the density of the fluid does not change with temperature variation, the height of the column of liquid can be determined from the pressure, liquid density and gravity.
In the medical field, differential pressure sensors are used for treatment of deep vein thrombosis, infusion pumps, and respirator and breathing detection equipment.
If you'd like to read more on other pressure measurement types then click the links below:
Looking for more on pressure sensor technology? Check out the further chapters of this guide below, or if you're pressed for time you can download it in a PDF format here.