4 factors steering connector choices in today's automotive applications
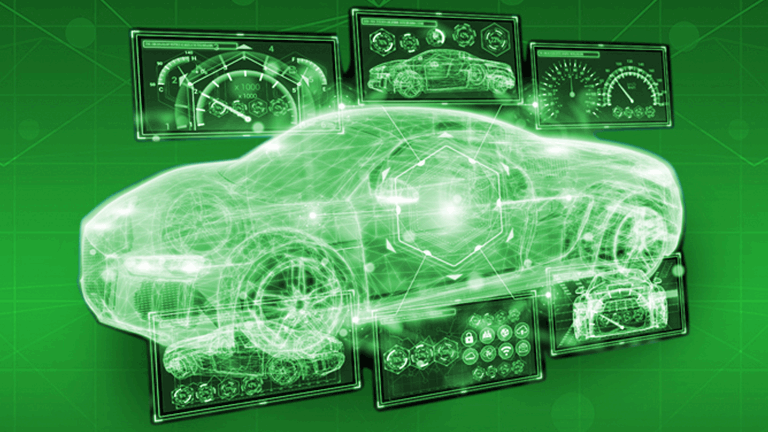
Each new generation of vehicles comes to market with an array of new electronic systems and gadgets. Some of these have replaced functionality that was previously primarily mechanically implemented. Others are completely new. Some, such as radar, are invisible to the driver while others, such as head-up displays (HUD), are visibly core to the driving experience. Regardless of the motivation and implementation, it is essential that the design aesthetic is maintained. This places automotive engineers under significant pressure to compress complex electronic systems into volumetrically limited spaces. Of course, none of this can be undertaken to the detriment of vehicle safety or reliability.
Over the past decade, incandescent light bulbs have largely been replaced with electronically controlled strings of LEDs or other solid-state luminaries. The mechanical hand brake has made way for the electric park brake (EPB), adding hill-hold as an additional feature over its mechanical predecessor. And even wing mirrors are being implemented with a combination of cameras and displays instead of mirrored glass. As well as having reliable connections to the vehicle’s power supply and electric/electronic (E/E) data networks, they often demand ultra-low-profile board-to-board or wire-to-board connections. Keypads and displays are also typically implemented as satellite elements connected to the central system via flexible printed circuit (FPC) or flexible flat cables (FFC).
1. Working with multiple boards
![]() Figure 1: The SlimStack FSB5 board-to-board connector offers 0.4mm pitch and a mating height as low as 5.0mm |
Integrating cameras and the associated image processing electronics into the same form factor, or smaller, used for wing and rear-view mirrors necessitates the use of a stacked multi-board approach. In addition to withstanding the shocks and vibrations of the automotive environment, the electronics and connector solution must deliver a reliable interconnect under a wide range of temperatures.
Such stacked printed circuit board (PCB) implementations need to carefully review the nature of the inter-board connectivity when selecting a connector solution. In the case of an imaging system, many of the signals will be low voltage, high-frequency and high in quantity. In addition, transfer of power will likely be required. Depending on the current being delivered, more than one connector pin may be needed to handle the power being transferred. Beyond the electrical parameters, it is essential to review the volume available in the housing and the real estate on the PCB. Even high density, low-profile board-to-board connectors with surface-mount pins can consume a surprising amount of PCB area, especially once keepouts due to other components or mechanics are taken into consideration (Figure 1, left).
2. Handling both power and signals with connectors
Figure 2: The Armor nail at the ends of these SlimStack board-to-board |
High-density connectors feature, by their very nature, large numbers of fine metal conductors. These are often optimised for handling low voltage signals rather than delivering power. Multiple pins can be used in parallel to handle power transfer, but board area, pin count and other constraints may mean that this is not viable. Selecting a connector dedicated to power delivery may be considered a suitable alternate approach but, with space at a premium and allowing for keepouts, a secondary connector solely for power delivery may not be an option.
In such situations it is worth searching out a multi-purpose board-to-board connector that has been optimised to handle both data signals and power delivery. Such solutions provide high-density gold-plated contacts for digital and analogue signals, while offering contacts with a larger surface area, such as a gold-plated ArmorÔ nail, that can handle several amperes of current (Figure 2). During the development process it is not unusual for elements of the application’s specifications to change, including the amount of space available for mounting. Often connector families provide a range of height options, allowing a move to a slimmer or thicker build height without having to change the PCB layout.
3. Maintaining connectivity under environmental extremes
Figure 3: 0.5mm-pitch FFC-to-board connectors (501786/501833/501784) |
Vehicles are operating under a variety of conditions across the world and their owners expect a hassle-free experience. This is regardless of whether they cruise the streets or spend their time off-road, live through freezing winters or the heat of equator summers. Connectors should be made of materials that undergo limited expansion and contraction over the extremes of temperature, while delivering uninterrupted signal and power delivery when subjected to vibrations and shock.
Despite their diminutive proportions, even the smallest fine-pitch connector offerings implement spring-loaded, multi-point contacts. Friction-locks and nail locks integrated into the connector also ensure a high retention force (HRF) for superior mating reliability. Selecting a solution with gold-plated pins ensures corrosion protection over the lifetime of the vehicle that, in turn, inhibits the formation of oxides that could impact the conductivity over time.
When connecting displays or satellite boards via FFC or wire-to-board connectors, designers often have a choice between, for example, vertical or right-angle connectors (Figure 3). This can often be helpful when surrounding plastics or a metal casing are impeding flex ribbon positioning. Cable tabs on flex ribbons are also supported by some FFC/FPC receptacles, providing a clear visual indication of correct alignment while increasing the retention force.
4. Connector selection for manufacture
Figure 4: Wire-to-board connectors, such as the Micro-Lock Plus series |
It is the little things that often make the difference and this is especially the case with connectors. Constructing such compact and dense electronics can be a challenge, especially when trying to align boards, or sliding an FFC or wire-to-board connector into a receptacle efficiently during manufacture. In order to ease mating of receptacle and connector, many connectors feature a wide alignment area. Once securely in position, they may also emit an audible click, providing reassurance of correct fitting even under blind conditions.
Features that simplify automated manufacturing processes should also be investigated, as these can significantly contribute to cost-savings during manufacture or improve long-term reliability. For example, some connectors include a nickel-barrier plating above the gold plating of the pins that prevents solder flux intrusion. And, despite their small size, many connector designs ensure enough flat surface area so that they can be pick-and-placed from a reel of product (Figure 4). Open top receptacles, combined with a polarisation key, can also ease fitting wire-to-board connectors.
FPC and FFC flex ribbon connectors also come in both back-flip and front-flip actuator variants. Depending on manufacturing constraints, consideration of one over the other may help to speed up construction and reduce quality issues that would otherwise arise due to incorrectly attached FPCs and FFCs.
Conclusion
While, on the surface, selection of the appropriate connector appears to be one of the simpler design decisions automotive engineers need to make, there is a lot more to be considered. The electronic system itself defines the number of connectors but it is definitely worth taking the time to consider the broad range of features connectors offer to improve the overall reliability of automotive electronics. From mounting and interconnect improvements, to reducing flux intrusion and providing an audible click, the optimal connector selection could deliver long-term reliability improvements and minimise quality issues.
As automotive technologies continue to develop, so will the connector requirements of in-car applications. We've teamed up with Molex and element14 for a webinar to further investigate the key automotive trends driving the need for micro connectors and take an in-depth look at the solutions available to engineers. Register for the webinar on element14, or if you would like to talk to one of our technical specialists click the Ask an Expert button to get in touch in your local language.

Ask an expert
Have a question? Our regional technical specialists are on hand to help.
