Making more efficient on-board chargers
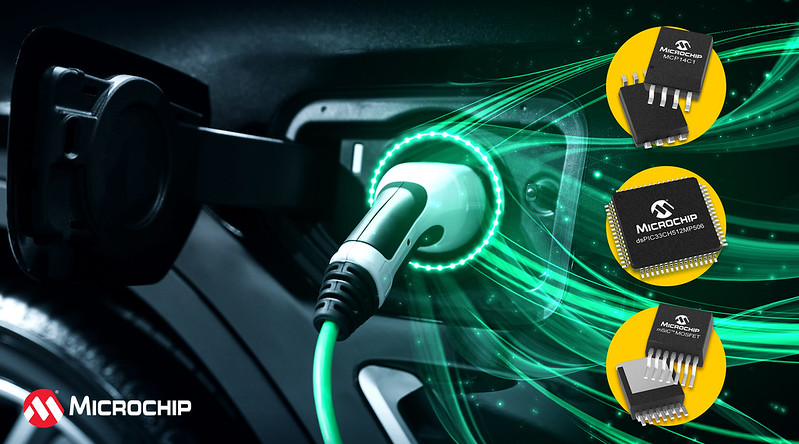
The process to convert potential energy or stored electricity, into motive energy or motion is a big deal. This type of power conversion is what makes the move to electric vehicles (EVs) possible. The entire world is transitioning toward the electrification of everything, and the most impactful areas are where fossil fuels currently dominate.
In order to keep pace with the rising demand of electricity, the way electricity is generated, transmitted, distributed and stored needs to transition from unidirectional toward omnidirectional power flow; that is power needs to be available anytime, anywhere. Distributed energy resources (DERs) play an increasingly important role but are typically far away from load centres. Renewable energy that isn’t used at the time of creation needs to be stored in and retrieved from energy storage systems (ESS) with high efficiency.
The battery technology being developed for EVs is impressive. Fundamental to the viability of the battery is its energy density. The tech world is making huge gains in that direction, by making batteries smaller and lighter, without sacrificing energy density. It’s not just road vehicles that are benefitting, look at the emergence of electric vertical take-off and landing (eVTOL) aircraft, electric railway, and heavy industrial transports like construction, mining, and farming vehicles.
Electric cars and busses may be one thing, but electric flying cars? They have an entirely different power-to-weight ratio to consider, with demand for ever increasing power density in lighter, smaller form factors. Regardless of the type of battery technology used, the need to quickly and efficiently convert electricity from one form to another remains a constant for effective battery charging.
There is a lot of conversion involved in the power domain. Electricity needs to be generated, transported and stored at the most efficient voltage and current levels to minimize losses before electrically is actually used to do work. Normally, those voltages are not compatible with the way it is eventually used.
The battery in an EV typically stores potential energy at around 400V or as high as 800V DC. To drive the motor, the DC voltage needs to be inverted to AC, depending on the motors used, turning the potential energy from the battery to kinetic energy of the moving vehicle. Auxiliary systems in that vehicle will still be running from 12V or 48V DC power rails.
Charging an 800V battery requires a potential of at least 800V DC, but our energy infrastructure doesn’t make 800V DC available at the outlet. This is where the on-board charger, or OBC, comes in. Some EV supply equipment (EVSE), more commonly referred to as charging stations, can deliver high-voltage DC direct to the car. Many more deliver single-phase AC voltage. The OBC takes the AC from the EVSE and converts it into DC, while also stepping it up to match the battery’s charging voltage. This is a complex process, one that can incur losses if converter efficiency is poor.
Those losses are experienced as heat and cost the consumer money. It’s like filling the gas tank of an internal combustion engine vehicle with fuel from a hose that has a leak. Now, for obvious reasons, service stations can’t allow leaky fuel hoses to be used, but there’s nothing in the rule book about inefficient OBCs.
Increasing OBC efficiency, out-of-the-box
The key to getting good efficiency from power conversion is having the right components in the right sockets. No single component can maximize total system efficiency, but one wrong component could bring it down.
Choosing a supplier that has a complete solution can be a real benefit. Better yet, if that supplier has already done a lot of the heavy lifting, then your solution could be optimized out-of-the-box. These reference designs have been system engineered by the supplier, using the supplier’s complementary products, to develop what is an almost turn-key solution.
Let’s look at a recent example. Microchip Technology has developed an OBC solution that brings together many of its automotive-qualified products, along with the embedded software modules that manage functionality, including AC-DC with power factor correction (PFC) and DC-DC conversion. This has the potential to significantly reduce and simplify the development cycle of an OBC application and speed time to market.
Microchip provides the key components for an OBC including the control, gate drive and power stage, as well as components for connectivity, security, sensors, memory and timing. The power stage component uses Microchip’s silicon carbide msiC™MOSFETs that include 700V, 1200V and 1700V mSiC products for 400V and 800V battery systems. These SiC MOSFETs can be used in the single or 3-phase AC-DC rectifier stage with power factor correction, and the DC-DC converter stage to step the voltage up to the higher level needed by the vehicle’s battery.
The DC-DC converter stage uses a step-up transformer, fed by a full-bridge DC-AC inverter. A full-bridge AC-DC converter rectifies the stepped-up voltage and feeds it to the battery. As there will be potential losses at every conversion stage, using SiC MOSFETs in each stage results in highly efficient conversion.
The complete solutions available from Microchip through Avnet Silica include a 3.8 kW/7.6 kW dsPIC33C totem pole converter and an 11 kW dual active bridge DC-DC converter. Both solutions are based on a dsPIC33 digital signal controller and mSiC MOSFETs/diodes.
To find out more about developing more efficient AC-DC, DC-AC and DC-DC converters, talk to one of Avnet Silica’s power experts today.

Sign up for the Avnet Silica Newsletter!
Stay up-to-date with latest news on products, training opportunities and more!
Need in-depth assistance for your design?
Avnet Silica's Online Technical Support Service
Helping you solve your engineering challenges




