How 48V systems are supporting fully electric vehicles
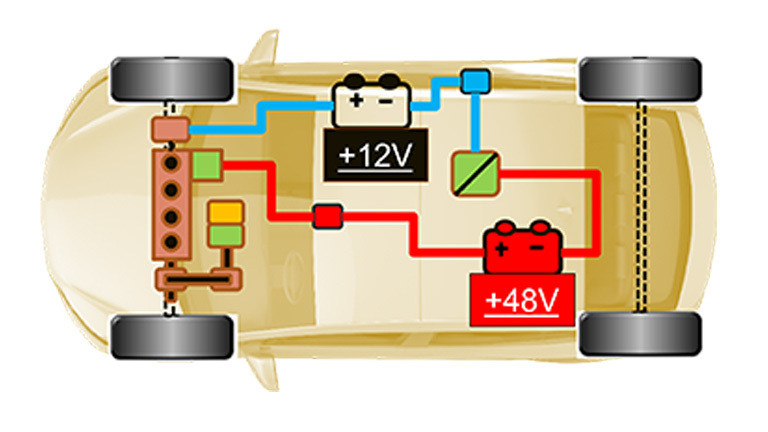
More consumers are moving toward battery electric vehicles (BEVs). Hybrid electric vehicles (HEV) and plug-in hybrid electric vehicles (PHEVs) provide convenience as the charging infrastructure develops. The mild hybrid continues to be a popular alternative.
All types of hybrid electric vehicles leverage the internal combustion engine (ICE) and regenerative braking to recharge the traction battery. All variants of hybrid and full electric vehicles feature inline electric traction motors, batteries and associated battery management systems. Each of these vehicle types continues to develop along their timeline from a common origin.
The battery voltages in HEVs, PHEVs and BEVs are around 200V to 800V. BEV battery voltages will be higher soon. This high DC voltage is essential to deliver the energy needed to drive the large electric motors used to provide traction. The electrification of traditional and supplementary auxiliary functions is accelerating. Automotive manufacturers have chosen 48V as the ideal intermediary power distribution system.
The ICE remains the only source of power in mild hybrids. They also use a 48V power architecture for both auxiliary functions and driving the traction motor. This keeps the cost and weight of the power distribution system closer to an ICE vehicle. The trade-off is that a mild hybrid has less powerful electric motors providing only supplementary assistance. Even so, mild hybrids can achieve a 10% reduction in carbon emissions. This compares well against the 4% reduction using start/stop technology.
The introduction of start/stop placed new demands on the electronic systems of ICE vehicles. The starter motor, normally used once per journey, operates whenever the vehicle stops. With a similar but more complex electromechanical device working with the ICE, the mild hybrid can be seen as the evolution of start/stop technology rather than a predecessor to PHEV of BEV.
Electric Vehicle Topologies
The 48V architecture powering low-carbon vehicles
Unlike the BEV and PHEV, the mild hybrid does not feature a high DC voltage architecture. There is no large battery and no onboard chargers required to convert AC from the grid. The mild hybrid configuration still uses a battery to drive the motor, and to capture and release kinetic energy through regenerative braking, but the voltage levels are lower at just 48V.
Using a 48V architecture reduces the cost of hybrid technology. The battery is smaller and therefore cheaper. The electric motor is also smaller. This simplifies the integration of mild hybrid technology into existing vehicle configurations.
At a system level, the 48V architecture is much more integrated into the vehicle’s subsystems than the very high DC voltages used in BEVs and PHEVs. The 48V subsystems are well-suited to all emerging vehicle types.
Standardizing on 48V for the electrification of mechanical systems creates a smooth transition to full electric for automotive OEMs. For this reason, the Tier 1 and Tier 2 automotive supply chain is rapidly transitioning to 48V subsystems.
A 48V power architecture is needed to support advanced driver assistance systems (ADAS) that require more power, such as steer-by-wire and brake-by-wire. Both 12V and 48V power rails are still required in all types of electric vehicles, so the power architecture must introduce a DC-DC converter designed to bridge the voltage divide.
DC-DC conversion in mild hybrid vehicles
48V for the mild hybrid starter-generator
The starter generator is a key component in the mild hybrid architecture. As the name suggests, this device will act as a starter motor running in continuous mode to supplement the traction provided by the ICE. It will also operate as a generator when coasting or braking.
The design of the starter generator will vary depending on where it is positioned in the drivetrain, but the motor will usually require three-phase AC power. This is converted from the 48V battery source. In reverse mode, the starter-generator will generate three-phase AC that will need to be inverted and regulated to recharge the 48V battery.
48V architecture in mild hybrid vehicles
The 12V and 48V power networks operate independently to supply different systems, but both are fed indirectly by the ICE through the starter generator. This means the two power networks must come together at some point. This is markedly different from other hybrid architectures, where the high-voltage system is isolated entirely from the low-voltage systems.
Designing a 12V-48V buck/boost converter
As well as having multiple voltage levels, electric vehicles also use multiple battery technologies. This will influence the design of the low-voltage networks and DC-DC converter. The voltage levels found in 48V automotive systems are defined by the standard ISO 21780:2020. This document is the first point of reference for engineers developing electrically powered devices intended to be used in a mild hybrid vehicle, for example.
A battery management system (BMS) will control both the 12V and 48V systems. An automotive-qualified microcontroller will be at the heart of the BMS. The MCU will monitor and dynamically control the DC-DC converter stage.
Redundancy, conversion efficiency and pulse-width modulation (PWM) control are all key elements of the BMS. The converter must operate in step-up and step-down modes to allow one battery system to maintain the other.
The choice of components will directly impact the performance and capability of the BMS and DC-DC converter. This includes selecting the most suitable integrated automotive power module (APM), MOSFETs and associated gate drivers. Electrically controlled disconnect switches must also be applied on both the 48V and 12V networks. Isolation can be handled by either optical or digital isolators.
OEMs will choose a converter topology that best meets their needs. For example, in high-power systems a multiphase converter topology would provide lower output ripple. This will also impact the size, weight and cost of the passive components used.
The design requirements of a 48V system for full and hybrid vehicles are numerous. To help engineers navigate these decisions, onsemi produced the free 48V-12V DC-DC Converter System Solution Guide.
This guide includes comprehensive support for automotive electronic design engineers looking to source the most suitable power components for 48V systems. This includes details of the APMs for 6-phase 3kW interleaved DC-DC converters, 2-channel back-to-back MOSFETs and 15-25kW inverter solutions.
As an example, the NXV08B800DT1 2-channel back-to-back MOSFET power module, rated for 80V, can be used in 48V mild hybrid applications as both a battery or load switch. The guide also includes details of onsemi’s Top Side Cooling Packages (TCPAK). This surface-mount device package uses top-side cooling to provide a thermal path through the top of the package and away from the PCB. This improves cooling and increases thermal density, resulting in a smaller overall solution.
Other innovations include onsemi’s T10 MOSFET shielded gate trench technology. This supersedes the legacy T8 trench gate technology and delivers lower on-resistance and gate charge, enhanced efficiency and reduced ringing.
Other technologies covered in the free 48V-12V DC-DC Converter System Solution Guide include electronic fuses to protect downstream 12V and 48V loads, peak current PWM controllers, and digital isolators. A list of technical documents provides easy access to additional resources, including reference designs, technical videos, and application notes.



