Three future Industrial IoT trends manufacturers should think about now
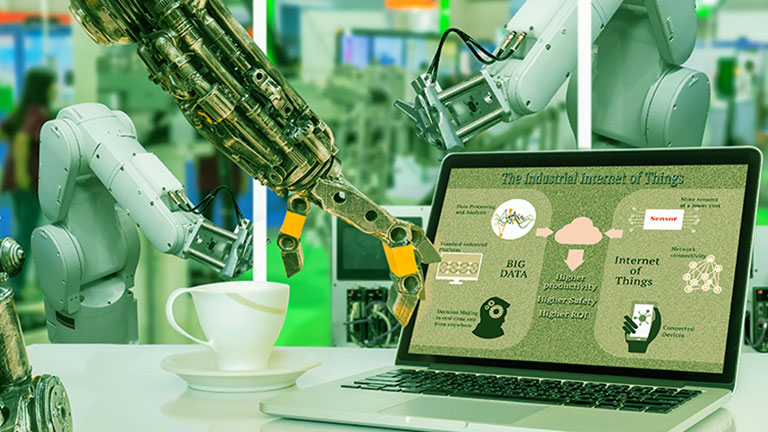
Independent reports show that acceptance of the IoT in industrial sectors is high. That indicates most organizations now have at least some experience of what the IoT can do for them.
But digital transformation is an ongoing process. Every day, new technologies appear that fit into the IoT. These developments generally aim to make IoT easier to adopt or help deliver greater benefits.
While some of these technologies may be point solutions with lots of competitive alternatives, some are more impactful at a much higher level. These are the technologies that create trends, and trends are what drive and influence the direction of advancement.
The acceleration of these trends is fueled by the much larger topics of AI and the IoT. Here’s why, in the industrial verticals where AI and IoT play, manufacturers can expect increased adoption in three areas: micromanufacturing, additive manufacturing and digital twins.
Micromanufacturing goes mainstream
The concept behind micromanufacturing involves scaling down the production volume. This contrasts with the much longer trend established around making factories ever larger. Mega and giga factories are all about economies of scale when making the same product in huge volumes. However, there is growing evidence to show that consumer demand is shifting away from mass production and more toward customized experiences.
This points to making things in smaller volumes with shorter production runs before redesigns take effect. Smaller production volumes mean smaller facilities and specifically ones that are more agile, able to respond to changing demands faster. It removes the issue of over-production, but because micro factories can be located closer to the end customer, some claim that it supports the move toward reshoring of manufacturing.
Micromanufacturing requires lower investment, less real estate and fewer resources. This makes it popular with new businesses, but established brands are also exploring the idea of micromanufacturing. Distributed manufacturing on a smaller scale, using local suppliers, creates a new tier in the economy that is almost entirely enabled by the new technologies found in the IoT.
It is largely dependent on technologies such as AI and advanced robotics because they are inherently reconfigurable and versatile. This allows more to be done with less machinery in a smaller physical area. In short, the Industrial IoT (IIoT) is fundamental to micromanufacturing.
Additive manufacturing supports on-demand manufacturing
Another key trend is the way additive manufacturing continues to supplement and, in some cases, displace conventional subtractive manufacturing and casting. This also supports the move toward more agile manufacturing in lower volume.
There are several advantages to additive manufacturing in a production environment. Apart from building to order, it also enables continuous improvement without wasting inventory, while also lowering the need for warehousing finished products.
As additive manufacturing equipment continues to improve, more manufacturers will be turning to this alternative approach to design and assembly. An additive methodology also makes it easier to consolidate multiple parts into a single assembly, providing further productivity gains.
Digital twins streamline supply chains
The third technology trend influencing the IIoT uses digitization to create a virtual representation of the real world. The data provided by the IoT allows the virtual world’s digital twins to operate just like the real thing. This means they react in a realistic way to both real and virtual changes controlled by an operator. The implications are huge, such as running various “what if” scenarios at high speed.
The concept behind digital twins is already established but the support needed to make it widespread is only now being rolled out. This includes a universal language to describe the built world in a way that is easy to model. For example, Microsoft’s Azure Digital Twin solution is based on its Digital Twin Definition Language (DTDL), which provides a common way of describing entire systems in a way that can be modeled and manipulated.
Digital twins will work on multiple levels. They will allow changes to production environments to be trialed virtually without causing disruption. As an example, the data captured from real devices can be used in accelerated lifetime testing to predict why and how something may fail. And by modeling entire supply chains, manufacturers will be able to see the consequences of unplanned disruptions and make contingency plans.
Partnerships make the IIoT work
All these trends are to some extent co-dependent. They rely on data, provided by the IoT, but they also build on the benefits that AI brings to the IoT. Micromanufacturing will devolve much of the control to AI systems, relying on them for scheduling, planning, resource management and logistics. Additive manufacturing brings new possibilities for shapes and structures that are currently not part of the engineer’s vocabulary. It is expected that a lot of the creativity needed to take advantage of these new possibilities will come from artificial intelligence.
The gains presented by creating a digital twin environment will be massive. Using data in an abstract way, to invoke real world activities, closes the loop on the IoT. It will redefine what we mean by cause and effect, because the cause could now be virtual while the effect will be real. And the result will also be much more predictable.
Realizing the advantages of these technologies will also emphasize the importance of distribution and a robust supply chain partner. Agile micromanufacturing goes beyond just-in-time, to something like everything-on-time. Managing that supply chain becomes much simpler when everything can be monitored, modeled and manufactured with greater resolution. This can be achieved using digital twin technology.
Avnet is a leading supplier of IoT solutions. Its products and services bridge the gap between hardware, software and the cloud. With over 2,000 engineers, Avnet is the one partner that can help its customers at any stage in their IoT journey and help bring everything together in a single, managed environment.



