Supply chain risk management: how to ensure business continuity
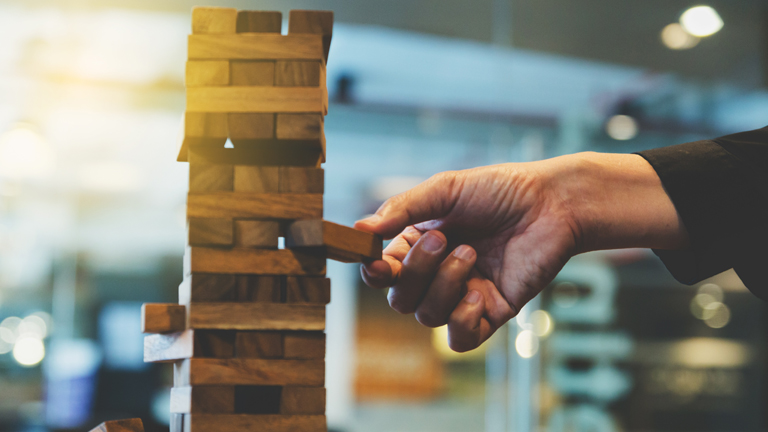
If the past few years have taught us anything, it’s that things don’t always go to plan. And nowhere have the effects of this been felt more than the global supply chain.
A pandemic wasn’t something many of us anticipated, but at the same time, we know we need to be prepared for unexpected events. Why then, did so much chaos and disruption ensue?
In order to make sure we can react swiftly, and effectively, when the inevitable happens, we need to have a good plan B. Or more specifically, in more jargonistic terms, we need to make sure we have robust business continuity plans if we’re to manage risk in our supply chains.
The show must go on
In practice, a business continuity plan looks at what can go wrong and what we can do to manage the risk and mitigate the impact if it happens.
Say one of your biggest warehouses is in Germany - what happens if the country goes into lockdown? Or the warehouse catches fire? Or you need to move stock from one country to another but one of your main transportation routes is blocked? There was a time when a major canal route getting blocked by a wedged container ship sounded unlikely. But hopefully we know better now.
Business continuity planning is about anticipating such weird and wonderful phenomena as international lockdowns and mammoth cargo ships throwing a spanner (or two) in the works. And it’s crucial if you want to manage the risk to your supply.
But we already tried plan B!
Now, some of you might be thinking ‘but we did have a plan B - it wasn’t enough’. And you’d be forgiven for thinking that. But we need to take it further, to something we in the MySupply team call (jargon alert!) Integrative Business Continuity Planning. Which is really just a fancy way of saying - what if other parties in your supply chain activate their Plan B at the same time?
Say your supplier usually ships from the Philippines to Singapore. There’s a ‘business as usual’ logistics flow and everything moves along swimmingly. But say you now need to change the delivery address. That disrupts the flow and potentially causes delays. Now imagine the supplier has a problem in the Philippines and they need to ship from Malaysia instead. The two new flows won’t easily synchronize and chaos is likely to ensue with, for example, products that would usually reach you quickly now stuck in customs for months.
If you add in things like the tax implications of traveling through a different country then the complexities, and disruptions, from what may have seemed like a couple of small changes really start to mount.
To take another example, what happens if your warehouse is halfway across the world from your production line and a lockdown is imposed? If you don’t have a Plan B, you’re in trouble.
Identifying the full extent of your risk
The first challenge is to understand what exactly your risks are. Whether you work with a partner (like us) or go at it alone, it’s crucial you look at things like interruptions to logistics flows, major geopolitical events or potential natural disasters (it’s surprising how many plants are built near volcanoes or on natural fault lines!).
How will they affect your ability to access or move stock? Will there be new protocols to navigate? Or tax implications?
Once you’ve figured out what your risks are, it’s time to start building in assurances in case they come to pass.
Beefing up Plan B. How to build assurances into your supply chain
Building in assurance is part of moving from the just-in-time production that so many of us are familiar with to more of a ‘just-in-case’ approach.
If you identify potential stock shortage issues down the line, can you call on your reserves? Or maybe you can strike a consignment deal with a distributor.
A distributor can supply OEMs with a store of inventory that isn’t charged for until it’s used. Consignment can help you hang on to your working capital until you actually need the parts required for your manufacturing process. So you’re at less risk of being stuck with surplus stock, but you know it’s there if you need it.
Another thing to look at is logistics. When some of our stock got stuck in the Suez canal, we were able to distribute via rail instead because we already had the necessary arrangements prepared as a back up.
Leaving no stone unturned
At Avnet, we have a dedicated risk centre that looks at potential risks to our suppliers by continually monitoring everything from seismic activity to changes in import laws, and geopolitical events. And we work with our clients to set up dedicated plans ready to action if things go wrong. And, if you need to, we can help you reroute materials through our own channels.
Whether you work with a partner or not, it’s imperative that you take a look at how you currently manage and mitigate risk. Ideally, you’ll leave no stone unturned when it comes to potentially disruptive events or issues in your supply chain.
And if you already have a Plan B, you can likely benefit from thinking beyond a self-centric model. What will other companies do when things go wrong? And how could that impact you too? So how will you then respond?
To be in as strong a position as possible when the inevitable happens, we need to start broadening our mindset and giving supply chain risk management the attention, and weight, it deserves.
We know that each change a business makes to its supply chain comes with risk. And we know there’s no one size fits all. So, if you'd like expert support with your supply chain challenges, please get in touch. We'd love to see if we can help.

Sign up for the Avnet Silica Newsletter!
Stay up-to-date with latest news on products, training opportunities and more!

/MYSUPPLY by Avnet Silica
Our supply chain architects get to the heart of your business, exploring your issues up and down the supply chain.


