IoT Smart Building: The Future of Construction catching up
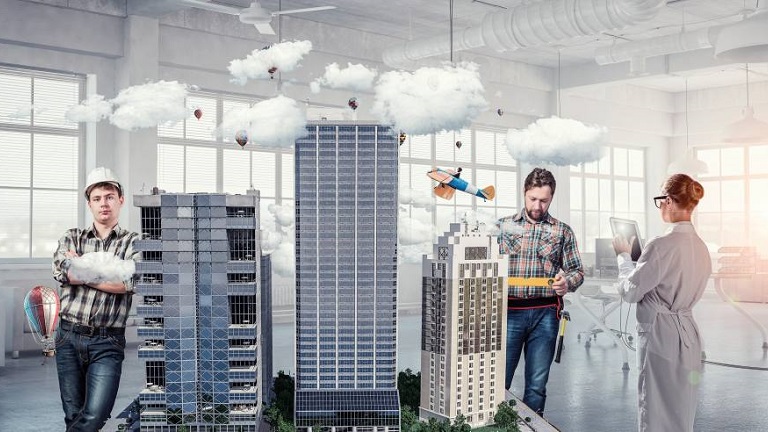
The building industry is older than the pyramids – and in many ways it has remained unchanged. However, after years of stagnating productivity and antiquated processes and procedures, construction is slowly awakening to the fact that, to remain viable, it needs to gamble big on technology in general and IoT in particular.
Construction holds the dubious honor of having the lowest prod industry, says a report by activity gains of any McKinsey & Company, a management consulting firm. In the United States, productivity in the construction industry has plunged by half since the late 1960s. UK newspaper The Economist called building the “least improved” of all major industrial sectors. Why?
Ask builders and they will complain about the rising costs of materials and increasingly restrictive building codes, along with tighter workplace regulation and many other suffocating bureaucratic strangleholds. Although low inflation in most developed countries has held costs down for the past ten years at least, over the same period productivity in construction in Europe and North America rose by just one percent annually – a piddling rate.
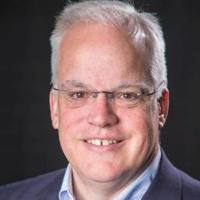
Robotics and 3D printing require 30% to 60% less building materials and can be completed between 50% and 80% faster.
Michael Shomberg, Global vice-president and general manager for engineering, construction, and real estate at SAP
To find an explanation for the anemic state of the building industry, one must search elsewhere, says Luc Luyten of Bain & Company, a consultancy firm based in Boston in the US. The first reason is that builders have been extremely reluctant to invest in technology because the industry has learned through bitter experience to always prepare for the next recession. Capital-heavy approaches to construction bring high fixed costs that are hard to cut during a downturn. “Workers, in contrast, can be fired,” Luyten explains.
As a result, construction relies heavily on brute force – in the struggle of machines versus humans, building workers have the advantage. This applies not only to less developed countries like India or Pakistan, where wages are low, but also to Western nations.
Fragmented market
The second reason construction lags behind other industries is its extreme fragmentation. In the US alone there are more than 730,000 building firms employing over seven million workers. That means the average head count of a construction company is just ten. The same goes for construction companies in most European countries. There are around 74,000 businesses in Germany employing 780,000 people, or about 10.5 people per company. The sheer number of firms presents a whole raft of problems, the greatest of which is cut-throat competition. With dozens of companies bidding on each contract, it is relatively easy for developers to drive prices, and margins, down. Even if a single winner emerges, the company will normally need to join forces with many other companies who are signed on as subcontractors, each looking out for its own best interests.
Digitalization, Luyten believes, is the only way out of this mess even though builders are slow to embrace digital technology. Take Building Information Technology (BIM), for example: its 3D modelling processes introduce efficiencies by allowing architects, engineers, and builders to work as teams, sharing information and harnessing the power of the cloud. In other words, BIM lets partners in a building project – architects, developers, contractors, and subcontractors – share files of information to support decision-making regarding a building or other built assets.
IoT Smart Building: Big BIM vs little BIM
In the past, builders relied mostly on 2D drawings (plans, elevations, and sections) to share information. Now 3D models provide a feel for the geometry of a building, and BIM makers have been busy adding extra dimensions, like time and cost, to their systems, causing many of them to refer to themselves as 5D BIM or Big BIM. Ideally, such systems go beyond the planning and design phases of the project, extending throughout the building life cycle and supporting processes including cost, construction, and project management as well as facility operation.
Critics have been quick to note BIM can’t do everything. For instance, date modelling with BIM takes much longer than something fresh off the drawing board, so more time and effort is required. At least theoretically, this should balance out in the end thanks to reduced costs due to errors and rectifications later. But for the construction company, feeding the necessary data – some of which might not even be available during the early stages of a project – means shifting effort, and investment, forward, with no certainty that anyone will eventually foot the bill or that any major benefits will accrue to the builders themselves.
Give and take: Members of construction teams need to share information more freely to get a complete picture of a project’s status and the steps that need to be taken next
Due to the fragmented, heterogeneous nature of the industry, widespread use of BIM faces additional hurdles. As a rule, many firms are involved in a project, each with its own software tools and computer-aided design (CAD) systems, and each with its own proprietary data format. BIM could solve the latter problem, but only if the functionality has been installed, and paid for, beforehand. In addition, many architects consider design as their own personal intellectual property and are highly reluctant to share data with others, even if they are all supposedly on the same team.
Digitalization is the future
In practice many building companies choose to opt for Little BIM – a stripped-down version that acts as a stand-alone solution with limited functionality. Its use is generally restricted to employees of one company or even one group within the company, such as planners or asset managers. Here, again, fragmentation means that builders hesitate to share costs with other companies, any of which could one day become their competitor.
Michael Shomberg, global vice-president and general manager for engineering, construction, and real estate at SAP, a German enterprise software company, is convinced the future of construction lies in digitalization. “From supply chain to workforce planning, digital technologies are bringing greater efciency and scalability to the construction industry,” he maintains. “Robotics and 3D printing, for example, require 30% to 60% less building materials and can be completed between 50% and 80% faster.” Shomberg has identifed fve key areas in which digitalization (IoT Smart Building) will transform the construction industry:
1. Expertise and knowledge
As a new generation enters the workforce and experienced craftsmen retire, there is an urgent need to make up for the resulting experience gap – if not, safety, efficiency, and productivity will be jeopardized. Construction, like all other industries, can expect to run up against a dearth of young, talented professionals who will be able to pick and choose their employers. These tech-savvy millennials expect digital rather than paper-based processes. On the other hand, the newcomers lack the experience and knowledge of their older colleagues – most of whom are heading for retirement. Builders need to adopt new ways and formats, such as tablet and smartphone apps.
2. Construction sites
Builders need to industrialize to survive. Many activities traditionally performed on site will be transferred to factory-like settings with greatly improved safety and efficiency. In these off-site “construction factories,” prefab modules can be made to much lower tolerances, at less cost and with better quality. These “Lego-like components,” as Shomberg calls them, will be moved to a construction site to be assembled by low-skilled workers – perhaps with the aid of wearable devices that make up for their lack of expertise by providing instant digital guidance and advice. Shomberg sees a future in which information from hyper connected smart sites will be gathered by sensors and continuously transmitted back to headquarters to provide real-time reports about building progress, allowing subcontractors to be paid sooner. This information stream will also be used to improve safety and reduce downtime, by anticipating and correcting problems before they occur.
Kid will be kids: Young, tech-savvy millennials expect digital rather than paper-based processes. Builders need to adapt fast to new ways and formats, such as tablet computers and smartphone apps
3. Project collaboration
Owners, contractors, architects, and other members of the construction teams will work on contracts which demand they share knowledge freely, and pay will be based on a project’s progress rather than individual performance. They will have access to information systems that give a complete picture of the project’s status and the steps that need to be taken next, including 3D drawings, job costs, as well as unstructured data, such as Word or Excel documents or manuals. This will virtually eliminate change orders, but more importantly, this kind of sharing will build trust and respect among team members, turning them into stakeholders instead of hired help.
4. Skill networks
In the social media age, Shomberg believes we will see the emergence of digitally networked workforces where skilled craftspeople will post their availability online and firms will search for workers based on their scores from former employers and clients. Workers will also be able to grade companies to alert future job seekers to employers that have been perceived as unfair. In this world of social networking, trade unions continue to play a role, Shomberg insists, primarily by implementing training programs to help members develop new skill sets and better understand new technologies.
5. Commissioning and operations
At the end of a building project, the handover of critical information must happen, and here digital systems could prove a boon. Information can be transmitted seamlessly from the developer to landlords or tenants without the need to re-enter anything manually. Data generated by BIM, ERP, or a project management system (PMS) can be linked at an early stage, thus reducing errors and the need for costly rectification and reworking. An added bonus is the ability to include information on warranty and maintenance of installed equipment, such as air conditioning systems or elevators, so owners will have access after the builders have gone. Most of Shomberg’s vision remains distant for most constructors. Things like digitalization of knowledge or networking closely with those who might become competitors is still anathema to many. People in construction seem to cling to their traditions, many of which would be recognizable to the guys who built the pyramids.

Sign up for the Avnet Silica Newsletter!
Stay up-to-date with latest news on products, training opportunities and more!

Take a DEEP look into the future!
Get the latest market trends and in-depth trainings on our Digital Event Experience Portal!

Avnet Silica Design Hub
Browse and review hundreds of proven reference designs to accelerate your design process. Our designs can be modified and saved in our AVAIL design tool and then exported to your CAD tool of choice.



