Yes, you can get to market fast in IoT
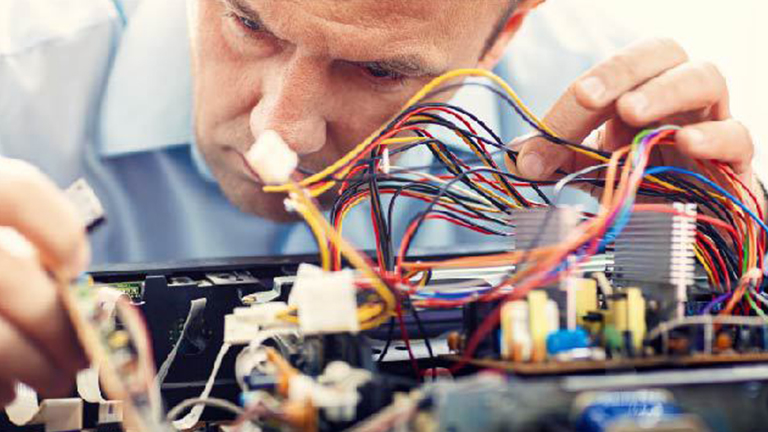
The Internet of Things (IoT) has been here for more than two decades, and it is still maturing. Technology is also evolving. What was difficult yesterday may be commoditized tomorrow.
IoT presents two broad areas of opportunity for OEMs. The first is to do the same thing they have always done but do it smarter using connected technology. The second is to do something new and innovative. Neither is the easy option; they both involve effort.
Adding customer value and making a good product are closely linked. OEMs must build a business model around the benefits of the IoT. Adding connectivity to an existing product isn’t necessarily going to win new customers. To make good business sense it must provide additional value to the customer. Using the IoT in the right way makes a real difference here.
Solving a customer’s problem at the source is good. Making the problem disappear is even better. Turning a customer’s problem into an opportunity for them is the ultimate objective. It requires cloud services that provide additional insights.
Should you build or buy?
Product design is familiar territory for OEMs. This is where your existing design engineering teams provide value. They can take a concept and turn it into a deployable product. Traditional embedded systems were about control. Closed loops provide that control, taking operational parameters as their inputs. The control algorithms run locally and are largely fixed by design.
Connectivity changed the shape of embedded systems. Long before the IoT, connectivity was already being used to share information and modify control parameters. The IoT introduced lower latency and greater visibility into embedded systems. Faster communications coupled with powerful cloud servers running analysis software redefined embedded control. Now, devices can be monitored and controlled in real time from remote locations.
The IoT is partly about using data to improve operational control and efficiencies. Almost any product can generate live data and any business case can use live data to increase the value of a solution. Actionable data comes from using live data to make operational decisions, often in near real-time, and relaying them back to the embedded system.
Although the data will be unique to an application, the hardware at the core of an embedded system can be generic. Adding sensors and actuators, along with the application software, turns a generic system into an application-specific solution. Generic functions include the processor, local storage, power management and communications. The generic nature of these functions means it can be fast and simple to use an off-the-shelf product. Adding sensors and actuators, coupled with the appropriate algorithms, rapidly turns generic hardware into an application-specific solution.
From single-board computer to system-on-module
Nothing defines generic like a single-board computer (SBC). For industrial applications, the SBC is more commonly referred to as a compute/computer module and based on either an x86 or Arm architecture.
The industry specifications for computer modules come from two prominent groups.
Standardization Group for Embedded Technologies (SGET) specifications include:
- SMARC
- Qseven
- embedded NUC.
PICMG (PCI Industrial Computer Manufacturers Group) specifications include:
- CompactPCI
- COM Express
- MicroSAM
The MicroSAM (Micro Sensor Adaptor Module) standard is relatively new and is intended to bring interoperability to boards based on microcontrollers from various suppliers, by providing a standard way to interface to common sensor types.
The concept of a common hardware platform has been adopted by semiconductor manufacturers to create the system-on-module, or SoM. Unlike an SBC or compute module, a SoM doesn’t conform to an industry standard, and they are not intended to be interchangeable.
SoMs provide an easy way to access the manufacturer’s processing technology by providing the ancillary features (such as power, connectivity, and memory) in a ready-made package. Using a SoM can save OEMs a lot of design effort.
Any module will generally need to be mounted on a motherboard or larger PCB. Those that follow an industry standard can provide an easy upgrade path to higher performance over the lifetime of the end-product.
Pre-certified wireless modules
Wireless communication is subject to certification even if the frequency used falls within the license-exempt range. Bluetooth and Wi-Fi are two of the most widely used protocols, but the IoT makes use of many others, including proprietary protocols.
RF is sometimes referred to as a ‘black art’ because it can seem like magic. As such it remains a specialist area of embedded design. Designing an RF frontend for an IoT endpoint at the component level adds little value but a lot of complexity to a product. OEMs that create their own RF solutions may struggle during the certification phase. Many may fail.
An alternative is to use one of the microcontrollers now available that come with integrated wireless connectivity. This removes the RF design complexity, however any product generating RF energy must be certified by the relevant regulatory body. Gaining certification is not necessarily difficult if reference guidelines are followed closely, but it needs to be considered.
The advent of pre-certified wireless modules provides an even simpler route to market. Although restrictions still apply and must be observed, it can be much faster and cheaper to use a pre-certified wireless module in an IoT product. Often the size and cost of the module will be comparable to a build-it-yourself approach and most of the certification risks and costs are eliminated.
Getting connected through a cloud platform
Designing an IoT endpoint is fundamental but connecting it to cloud services is the most important part. This is the best example of where buying makes much more sense than building.
Attempting to replicate the features offered by commercial IoT cloud platforms would be an enormous task and offer no real differentiation. It only provides a return on investment if the OEM sells the cloud platform as a service. For most, this is not the revenue stream they are looking to generate nor an infrastructure they wish to develop and support.
Some commercial cloud platforms bundle all their functionality into a single interface. This was likely modelled on the way most people used the internet, through a small number of ports associated with email, web browsing and streaming. Domestic, human-centric web interactions favor downstream traffic.
An IoT application is different. It will be opening and closing ports much more frequently and have a more balanced data transfer profile. To provide for this, modern cloud platforms are built on microservices. If a particular microservice is in high demand the cloud platform can deploy more instances of that microservice to meet demand. Overall, it takes fewer valuable resources to deploy individual microservices than complete service packages, so the cloud platform can make better use of its resources.

Modern IoT platforms provide the critical part of a connected product offering
Scaling up in the IoT
Modern IoT cloud platforms must be configured for scalability. The IoT is projected to reach hundreds of billions of connected devices. A cloud platform able to manage that many individual connections must be scalable and global.
Cloud platforms such as Amazon Web Services (AWS) and Microsoft Azure now use a microservice based architecture. Microservices provide this scalability, along with all the flexibility and configuration an OEM needs. However, customers need expertise of the underlying microservices to create a managed product experience.
OEMs need to appreciate this. They will need to implement the application programming interfaces, or APIs, that communicate with the cloud platform’s microservices. Every feature of the cloud platform will have an associated microservice, and every microservice used by an endpoint will require an API.
Taking a build rather than buy approach to cloud platforms extends to creating these APIs. If an OEM chooses to code each API to a microservice they must also choose to integrate and test those APIs. Again, this adds little value to the OEM’s overall proposition.
The alternative is to leverage a product like IoTConnect from Avnet Silica. IoTConnect is solution acceleration software, which means it provides pre-enablement of IoT cloud platforms. Avnet Silica has already integrated IoTConnect with Microsoft Azure and is in the process of integrating it with AWS.
The APIs developed for IoTConnect are portable and easily integrated into an OEM’s endpoints. By choosing this route, OEMs require less development, less integration, and less testing. Communicating with a cloud platform’s microservices becomes much simpler.

IoTConnect from Avnet Silica provides a simpler interface to IoT cloud platforms, as well as making it easier to productize IoT services. The ability to integrate value-added features is also important.
Avnet Silica has packaged this pre-enablement into accelerators. Each accelerator targets a vertical market, such as smart city, or factory automation. OEMs can use an accelerator as the basis for their own application. And because the accelerators are fully formed, some OEMs will not need to add any further functionality.
With a wide portfolio of SBCs, pre-certified wireless modules, control systems and the IoTConnect acceleration software suite, Avnet Silica can approach an IoT solution from any aspect and offer value at every point. This approach has been developed in direct response to the way the build versus buy balance has changed over time. Complexity and demand for advanced features has created a need for off-the-shelf solutions. All OEMs need do is work with Avnet Silica to define the application, configure the customer dashboard, and start deploying.
The IoT needs an ecosystem
Another important aspect to consider is the additional features, functions, and services an OEM’s IoT offering will need to provide. This is where buying is almost the only route to market. Adding services such as face recognition using AI, or predictive maintenance using machine learning, can be extremely valuable to an OEM and their customers. Developing these features and then integrating them into the solution is a huge task.
The recommended approach is to partner with experts in their field to provide these features. This larger ecosystem can be managed by the OEM, but again this is not a value-add for the manufacturer. Accessing an ecosystem of suppliers is the right way to go, but this too needs managing. Avnet Silica has built this into IoTConnect, through its Partner Engine, which provides easy access and integration to a growing number of partners that can offer these additional value-adding features.
Conclusion
The build versus buy decision has previously been about cost. For the right application in the right volumes, it can be cost-effective to design everything in-house. Complexity, from the board to the cloud, is changing the balance.
OEMs will continue to innovate, keeping a lot of design in-house. This makes sense from an engineering and business aspect. But the real value-add that comes from the IoT takes more than just good engineering. It starts with the endpoint, but it rapidly extends to the value proposition. That value comes from leveraging existing, proven solutions that can accelerate your time to market. It also comes from accessing the very latest and best-in-class solutions from an ecosystem of suppliers focused on making you more successful.
DISCOVER MORE ABOUT IoT CONNECT AND AVNET SILICA'S POWERFUL IoT PRODUCTS AND SERVICES



