A closer look at SiC quality
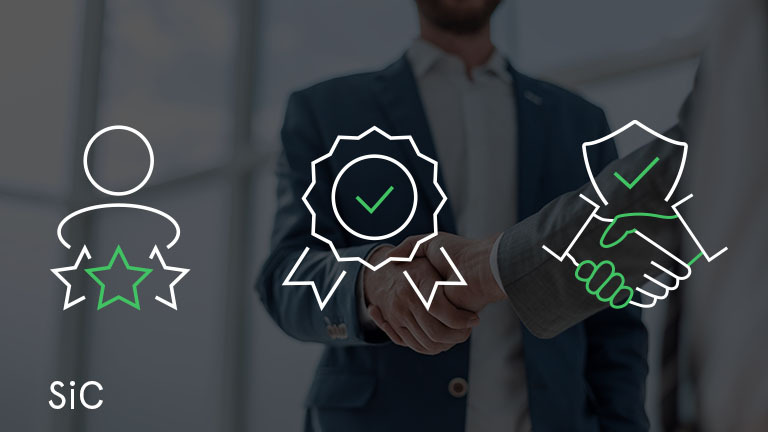
Two of the largest markets for medium- and high-power electronic components are industrial and automotive. The move to e-mobility is perhaps the single biggest development in decades to influence how semiconductor vendors have invested in their technologies.
With incumbent technologies such as IGBT sitting beside new developments in silicon carbide (SiC) and gallium nitride (GaN), engineers have the capability to develop more efficient and effective power solutions for industrial, automotive and other areas where electrification is reshaping applications.
Developments in SiC diodes and MOSFETs, and subsequently power modules, are benefiting any application where motor drives and inverters are a key differentiator. This applies in both the physical size of the equipment and operating efficiency. With measurably better performance, SiC diodes and MOSFETs are complementing and sometimes displacing IGBT MOSFETs and SuperFETs in various power supply topologies.
The energy infrastructure now describes how renewable energy is being captured, stored and used. Energy storage systems are seeing around 17% annual growth and are being deployed to supplement and support the existing power grid, using energy captured through solar, wind and other renewable sources. Solar power is also seeing double-digit growth thanks to the continued development of photovoltaic technology and the use of new semiconductor compounds to make better use of the energy they capture.
The energy infrastructure

Wide bandgap power semiconductor technologies including SiC are redefining the energy infrastructure. (Source: onsemi)
With e-mobility seeing the largest compound annual growth, around 26%, the electric vehicle charging infrastructure is a consumer of energy. But even here the use of bidirectional and vehicle-to-grid technologies are changing the way the energy infrastructure works.
These trends focus attention on the efficiency with which energy can be generated, transferred and consumed. Silicon carbide is the leading semiconductor technology engineers are leveraging to increase power density, conversion efficiency and overall efficacy of the energy infrastructure.
Where SiC works best
There is no single technology for all power applications. By developing a growing portfolio of SiC-based diodes, MOSFETs and power modules, onsemi now offers solutions that work together to provide the best solution for any given requirement.
Working with Avnet’s own engineers, onsemi can advise customers on where and how to use its SiC solutions to get the best performance. This includes onsemi’s M1, M2 and M3S SiC MOSFET families. The M1 family covers 1200 V and 1700 V and feature large die areas to lower thermal resistance, providing a balance between switching and conduction losses. The M2 family covers 650 V, 750 V and 1200 V, with a design optimized for the lowest on-resistance (RDS(ON)), making them more suitable for low-speed applications. The M1 and M2 families are being used in DC-DC solid state relays and traction/motor drive circuits. The M3S family is designed for high-frequency switching, making it the better option for hard switching and LLC resonant applications.
SiC diodes, including onsemi’s D1, D2 and D3 families, also deliver the benefits of silicon carbide, such as low thermal resistance and high switching speeds. These devices are being designed into Vienna rectifier input stages, PFC stages and output rectification. They also cover operating voltages from 650 V to 1700 V.
Building quality into the SiC supply chain
The supply chain for traditional silicon substrates is mature. This maturity comes from many decades of manufacturing data that can be used to further improve the processes used. Silicon carbide, while based on silicon, is significantly different from silicon. Although the industry has leveraged its experience, every stage of the manufacturing process is specific to SiC and has been developed according to the unique characteristics of SiC.
Defects are the enemy of the integrated device manufacture. The slightest flaw can render a device inoperable and is why the subject of yield is so important. A higher yield leads to a lower cost to the customer. This is where onsemi has focused its efforts to detect and remove defects at every stage of the manufacturing process.
Semiconductor manufacturers use the classic bathtub curve to characterize the three stages of a device in terms of failures. These comprise early or infant mortality, which includes failure due to the manufacturing process, the operational or steady state mortality, and the ageing or wearing out of the device. Manufacturer data is used to predict and improve quality and reliability at each of these stages. Typically, the bathtub shape is the result, indicating a reduction in mortality at the infant stage and the inevitable increase in mortality as the device ages.
Many factors impact quality. Because silicon carbide is much less mature than silicon, there is less manufacturer data to help influence quality. Manufacturers leading in this area, which includes onsemi, are actively contributing to the development of quality practices for SiC.
A key part of improving device quality is managing the epitaxial layer. This is the layer where much of the device’s operating characteristics are defined and controlled. Part of onsemi’s commitment to producing high-quality SiC devices includes the development of its own epitaxial layer technology. This is a key differentiator for onsemi and helps position its devices at the forefront of the industry.
Modeling is used extensively in the semiconductor manufacturing industry, and onsemi has developed its physically based, scalable SPICE modelling methodologies for modern power electronic devices. It has used its expertise to adapt existing power models to make them applicable to SiC devices. This approach creates a direct link between SPICE, physical design, and process technology.
SiC needs an end-to-end supply chain
Maintaining a high level of quality and reliability in SiC manufacture comes from taking control over the processes involved. The leadership onsemi has established is based on five pillars of the SiC ecosystem and through acquisition, onsemi is now a fully integrated SiC manufacturer. This starts with making the SiC boule and slicing it into wafers. At this stage onsemi applies its epitaxial layer to define the semiconductor characteristics. The wafers with epi layer are processed using planar technology, with trench technology in development. Once processed, the wafers are diced ready for packaging to create diodes, MOSFETs and modules
Real-world testing ensures long-term reliability

Using repetitive continuous operation testing, onsemi can guarantee the quality of its SiC devices. (Source: onsemi)
In addition to product reliability testing, onsemi carries out defect scanning both before and after the epitaxial layer is grown. All dies are 100% avalanche tested, which identifies potential failures. Product level burn-in is also carried out, to remove extrinsic gate oxide failures.
Repetitive, continuous operation testing creates a real-world application to put devices through realistic functional testing. This includes operating the devices at various voltages and switching frequencies, junction temperatures in continuous conduction mode with hard switching.
Because SiC crystals have defects, visual inspection is also used to find wafer defects. Other tests include avalanche testing and extensive burn-in. Any contaminants between the silicon carbide and silicon oxide are detected as early as possible. Burn-in is also used at wafer level and to test the final products. This stresses the gate voltage at high temperatures, which guarantees the quality of the products shipped.
Quality is fundamental to the semiconductor industry. Detecting defects as early as possible, wherever they are introduced, is critical. With its end-to-end supply chain, onsemi has successfully implemented industry-leading quality procedures at every stage of the SiC manufacturing process.
With this level of quality, Avnet Silica and onsemi are ready to meet your power semiconductor requirements. To find out more, contact your local Avnet Silica representative.
onsemi
SiC Solutions
onsemi and Avnet Silica provide your direct path to reliable silicon carbide solutions, driving higher efficiency at every stage.




