Choosing analog sensor and power management parts for factory automation smart sensor nodes

The past three decades have transformed the industrial automation market. Increasing production efficiency relies on a host of sensor nodes to gather real-time information crucial to the control systems. Sensors collect essential parameters from the analog world, ranging from environmental conditions such as temperature, humidity, and air pressure, for conversion into the digital domain. Other sensors are used to determine position, for example, the angular position of an industrial sensor arm and to detect the presence and concentration of specific gases used in a factory process.
The sensor's output signal directly impacts the operation and performance of the factory automation system, so it needs to be accurate, stable, and reliable. Also, because many remote sensor nodes may be battery-powered, the sensor must report on its own performance.
This article looks at some fundamental technical considerations when selecting analog sensor and power management components used for factory automation applications.
Factory automation systems rely on smart sensor nodes
Sensors are a vital component of any industrial automation machinery. They provide the critical feedback signals for the control loop functions that drive the machine's operation. The term sensor describes the whole sensor, perhaps a highly integrated module, and the individual sensor element that performs the sensing function. Often the term is used interchangeably. Sensors cover many measurement criteria, from environmental factors such as temperature, air pressure, and moisture to absolute and relative three-dimensional positioning information. Mechanical sensors measurements include compression, torsion, tension, bending, and shear forces.
Consider an industrial robot used on an automotive assembly line. Typically, a robot can change its tool head, termed an effector. The robot's body may move only in one direction, while its arm can move in three dimensions. Each effector will have a set of parameters unique to its function. For example, an effector that picks up a delicate item, say a door mirror, has to grasp it firmly enough so it doesn't drop it but not apply too much pressure such that it damages the plastic housing. Precise, accurate, and fast pressure sensing of the effector's gripper fingers and instant feedback to the gripper's actuator drive circuitry is imperative.
Key characteristics of a sensor
Although sensors may serve many different measurement functions, they all have a similar functional architecture. Figure 1 highlights the primary circuit functional blocks of a sensor.
Figure 1 - The major functional blocks of a sensor node used for various industrial automation applications (source ST)
The left-hand side of Figure 1 highlights the power supply options. Some sensor units take their power from the host application, the industrial robot in the above example. Others may operate from a replaceable or rechargeable battery or harvest energy from ambient sources and store it in a supercapacitor. Each approach has a set of common design considerations, and some only apply to one. For example, using a battery will require monitoring the battery's state of charge to determine when to schedule a replacement. A requirement common to the battery and line-powered methods is the conversion and regulation from one voltage to another. Analog and digital circuits typically require different supply rails, requiring the voltage regulated within defined specifications.
Depending on the system architecture, it may utilise analog or digital sensors. An analog sensor outputs an analog voltage relative to the measuring parameter. Most sensors exhibit a positive response, so the output voltage increases with temperature for a temperature sensor. A temperature sensor typically incorporates the core analog temperature sensing element, an analog to digital converter, and optionally, an embedded microcontroller (MCU). The MCU may linearise the analog output signal and handles communication to the host system via a popular interface such as I2C, UART or SPI. Signal conditioning is an essential aspect of any sensor type, improving the signal integrity and removing unwanted harmonics, transients, and other artefacts.
Sensor accuracy, in terms of precision and measurement repeatability, together with keeping signal noise to a minimum, is vital for most applications. Noise in a control loop may introduce 'jitter', resulting in poor machine performance. Poor measurement accuracy may sometimes cause the robot to misalign itself, potentially causing damage to the workpiece.
With energy efficiency a hot topic for all organisations today, keeping the power consumption profile of every circuit is vital, and this aspect is essential for battery-powered applications.
Power management functions
Low-dropout regulators
Low-dropout regulators (LDOs) are a popular method of regulating the supply voltage to a circuit. Unlike switching converters, they are straightforward in design, making them compact, exhibiting low noise characteristics, and are relatively low cost. They offer a convenient method of providing regulated DC voltage to the load from higher DC voltage source, being that AC-DC converter output, battery or higher voltage system DC rail. Of particular note, the efficiency of an LDO is directly linked to the difference between the input and output voltage, where a higher difference means a lower efficiency. However, unlike switching converters, they cannot provide an output voltage higher than the input.
Figure 2 illustrates an LDO's internal design.
Figure 2 - A schematic of an LDOs internal functions - this example is the ST ST730 300 mA 28 V low-dropout regulator (source ST)
The example LDO is the fixed output variant of the ST730 from STMicroelectronics (ST). An op-amp output drives the gate of a transistor with its source and drain connected between Vin and Vout. The op-amp's positive input is biased with a bandgap reference voltage, while the negative input tracks the Vout using a resistive divider. The output signal from the error amplifier is used to change the gate voltage of the pass element to maintain Vout at the nominal value.
The ST730 is also available with an adjustable voltage range, which replaces the internal voltage divider with user-configured external components. An enable pin allows a host application to switch the output on/off using digital logic. The device has an ultra-low quiescent current characteristic of 5 µA.
Understanding some key LDO terminology helps engineers select and specify suitable devices for their design. Terms include:
Dropout voltage: The difference in input-to-output voltage beyond which the LDO can no longer regulate the output against further input voltage reductions. To maintain the nominal Vout, Vin must be Vout + the dropout voltage.
Quiescent current: This is the current required to operate the LDO's internal functions. Current is consumed by the op-amp, the bias generator, the band-gap reference, and the voltage divider irrespective of the load's status.
Load regulation: The ability of the LDO to maintain a constant Vout despite changes in the load condition. Load regulation is expressed as a percentage-wise change in output voltage relative to the change in load current.
Line regulation: Line regulation is expressed as a percentage-wise change in output voltage relative to the change in input voltage.
Power Supply Ripple Rejection (PSRR): An essential measure of an LDO's ability to filter out ripples on Vin and prevent them from becoming noise on Vout. PSSR is specified across a range of frequencies and stated in dB.
For more terminology explanations and a guide to the range of LDOs available from ST, a Quick Reference Guide is published here.
Voltage monitoring
As highlighted earlier, in battery-powered designs, measuring the battery's output voltage indicates its state of charge (SoC). For any given battery chemistry, the manufacturer will publish a chart detailing the battery's state of charge (SoC) percentage against voltage. This chart can be used to gauge the battery SoC against gauge icons, 25%, 50%, etc. However, the measurement circuit must not impose a load on the battery such that it actively contributes to the device's overall current consumption.
Figure 3 showcases an ST op-amp configured for a battery voltage monitoring application.
Figure 3 - The ST TSU101 nano power op-amp measuring the battery voltage (source ST)
The ST TSU101 only consumes 580 nA per channel, which imposes a minimal load on the battery. It is 5 V rail-to-rail capable on both the inputs and output. It is ideal for use in battery-powered applications where long service life between battery changes is crucial. It is available in both single, dual, and quad package variants.
Sensor node analog signal chain considerations
Op-amps are ideal conditioning components for an analog signal chain. Their low power attributes, small size, and application flexibility characteristics are highly beneficial. However, some use cases call for the use of precision, low noise op-amps. A couple of op-amp factors make them stand out for such applications, so an understanding of these factors can assist an engineer in selecting suitable parts.
The characteristics of an ideal op-amp include infinite gain, an infinite input impedance, and a zero-output voltage when the inputs are exactly the same.
Input offset voltage
However, in the real world, the actual specifications differ slightly. For example, most op-amps exhibit a small output voltage even when the two inputs are the same. Unfortunately, the nature of an op-amp is that any input signal difference is amplified and results in an output voltage, so any erroneous voltage, is amplified, too. To cancel out the output voltage error, a small differential voltage needs to be applied to the inputs to reduce the output voltage to zero. This voltage is termed the input offset voltage (Vio).
The input offset voltage occurs due to slight mismatches during IC fabrication. There might be doping variations of the semiconductor material, lithographic errors, or the result of packaging stress during assembly and test. Each op-amp will exhibit slightly different Vio characteristics.
The impact of Vio in closed loop amplifier will reflect in presence of Vio DC voltage between positive and negative amplifier inputs. Unless an additional biasing differential offset voltage is applied, it will result in an output error. For example, in a motor speed control application, where an op-amp provides a feedback signal to the motor speed controller, the motor's actual speed will differ from the calculated speed. This error may be highly critical for some applications. Figure 4 highlights how Vio impacts reading current sensing on a motor drive feedback control circuit, showing a Vio of 5 µV.
Figure 4 - The impact of Vio on current sensing for a motor speed control feedback loop application (source ST)
For precision applications, evolving higher frequency sensor, an op-amp with a low input offset voltage and high bandwidth should be selected.
Sources of op-amp noise
There are multiple sources of op-amp output voltage disturbances, ranging from noise from the internal circuitry, propagation of input common mode signals to the output, to propagation of power supply voltage changes to the output. Op-amp characteristics that are quantifying these phenomena are the common-mode rejection ratio (CMRR), the power supply rejection ratio (PSRR), and the equivalent input figure.
Common-mode rejection ratio (CMRR): Expressed in dB, the CMRR defines the ratio of an op-amp's common-mode gain compared to its differential-mode gain. If a differential input voltage of Div produces an output of 1 V, and a common-mode change of Civ produces the same output voltage, then the CMRR is Civ/Div. It is typically plotted against frequency, with most op-amps CMRR tailing off at higher frequencies - see Figure 5.
Figure 5 - The CMRR characteristic of the ST TSV7722 op-amp against frequency (source ST)
Power supply rejection ratio (PSRR): The PSRR specifies how much an op-amp's output voltage changes with changes in the supply voltage. An ideal op-amp would not exhibit this behaviour, but the reality is that most op-amps will display some change in the output.
Equivalent input noise: All noise generated from op-amp as an integrated circuit, coming from various sources like thermal. Shot, flicker, burst and avalanche noise can be represented by equivalent input voltage and current noise. In case of equivalent input noise voltage (en) it is defined as output noise level divided by amplifier small signal differential gain and is expressed in V⁄(√H z).
Precision analog components are essential for factory automation smart sensor nodes
In this short article, we've highlighted just some of the vital analog functions of a typical smart sensor. Selecting the right components for these applications is crucial to developing a reliable and trustworthy design.
An authorised STMicroelectronics distributor, EBV offers a comprehensive portfolio of low power, low noise, and precision analog components.
Discover ST’s analog portfolio and find more application examples
About Author
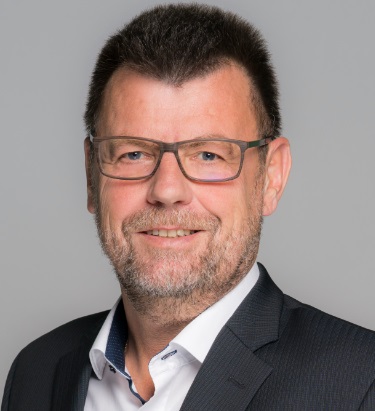
Karl Lehnhoff joined EBV Elektronik in 2008 as a regional application manager. From 2011 till 2019 he headed the renewable energies segment, today called city and infrastructure, as a director. He has served in his current role since March 2019. Previously he held multiple different roles in R&D, field application engineering and field sales. He has a degree as Dipl.-Ing. (FH) in electronics from University of Applied Sciences in Dortmund.



